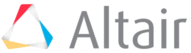

Catalog excerpts
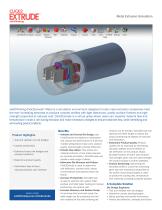
EXTRUDE solidThinkinjf Metal Extrusion Simulation Orient Model Flow Volume Organize Billet Extrusion Move Push/Pull Tools solidThinking Click2Extrude™ Metal is a simulation environment designed to help metal extrusion companies meet the ever increasing demands to produce complex profiles with tight tolerances, quality surface finishes and high strength properties at reduced cost. Click2Extrude is a virtual press where users can visualize material flow and temperature inside a die during extrusion and make necessary changes to ensure balanced flow, while identifying and eliminating product defects. Product Highlights • Test and validate new die designs • Improve productivity • Optimize/correct die designs and process conditions • Determine product quality • Automated, easy to learn, extrusion-specific user interface Benefits • Validate and Correct Die Design: Use Click2Extrude simulations to understand and improve the performance of a die from multiple perspectives (nose cone, product quality, weld strength, process efficiency). • Extrude New Alloys: Flow stress and material behavior of new alloys requires an accurate simulation. Click2Extrude can handle a wide range of alloys. • Determine Die Stresses and Failure: Click2Extrude is used to determine tool deflection, mandrel shift, stress concentrations and potential early die failure. • Increase Productivity: Click2Extrude is used to optimize ram speed, billet preheat and billet taper heating to improve productivity and reduce cost. • Increase Recovery and Reduce Scrap: To minimize front and back scrap, the weld length can be computed and the skin material of the billet entering the product can be tracked. Click2Extrude can optimize the billet length to reduce the scrap considering all aspects of extrusion and fabrication. • Determine Product Quality: Product quality can be improved by eliminating extrusion defects and the effects of die deflection on the product shape. By determination of seam weld location and strength, grain size and yield strength the product quality is further assessed. • Analyze Quenching: Quenching the extruded profile is crucial for controlling grain size and mechanical properties of the profile. Quenching analysis is used to predict the cooling rate, temperature and uniformity of cooling during the process. A Complete Solution Die Design Engineers: • Test and validate new die designs • Determine correct bearing lengths • Adjust porthole and pocket dimensions • Predict die deflection, stresses and
Open the catalog to page 1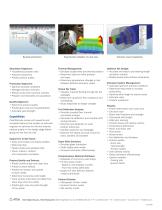
Simulation Engineers: • Troubleshoot problem dies • Improve productivity • Predict product quality Production Engineers: • Optimize process conditions • Manage extrusion inventory • Reduce scrap and maximize recovery • Prepare cost estimates and quotations Quality Engineers: • Determine product quality • Predict grain size and recrystallization • Calculate yield strength Capabilities Click2Extrude comes with powerful and complete features that enable an extrusion engineer to optimize the die and improve product quality in the design stage before going into the first die trial. Support for...
Open the catalog to page 2All ALTAIR catalogs and technical brochures
-
solidThinking Activate
2 Pages
-
solidThinking
2 Pages
-
HyperWorks Unlimited ®
2 Pages
-
Evolve ®
2 Pages
-
HyperView ®
2 Pages
-
HyperMesh ®
2 Pages