
Catalog excerpts
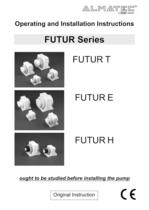
Operating and Installation Instructions FUTUR Series FUTUR H FUTUR E FUTUR T ought to be studied before installing the pump Original Instruction
Open the catalog to page 1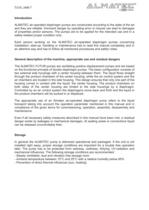
FUTU R · page 3 Introduction ALMATEC air-operated diaphragm pumps are constructed according to the state of the art and they are reliable. Imminent danger by operating error or misuse can lead to damages of properties and/or persons. The pumps are to be applied for the intended use and in a safety-related proper condition only. Each person working on the ALMATEC air-operated diaphragm pumps concerning installation, start-up, handling or maintenance has to read this manual completely and in an attentive way and has to follow all mentioned procedures and safety notes. General description of...
Open the catalog to page 3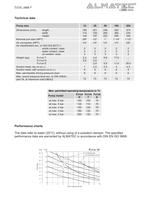
FUTU R · page 4 Technical data Pump size 10 20 50 100 200 Dimensions (mm), length width height 185 114 130 201 150 167 246 200 222 303 260 265 374 330 345 Nominal port size (NPT) 3/8“ 1/2“ 1“ 1 1/4“ 1 1/2” Air connection (NPT) Air classification acc. to ISO-DIS 8573-1: solids content, class water content, class oil content, class 1/4“ 2 3 3 1/4“ 2 3 3 1/4“ 2 3 3 1/4“ 2 3 3 3/8” 2 3 3 Weight (kg), FUTUR T FUTUR H FUTUR E 2,3 2,6 - 4,2 5,0 2,8 8,8 - 5,8 17,6 - 11,8 - - 29,0 Suction head, dry (m.w.c.) Suction head, with product (m.w.c.) 1 8 2.5 9 3.5 9 4 9 4,5 9 Max. permissible driving...
Open the catalog to page 4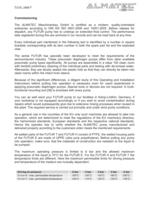
FUTU R · page 6 Commissioning The ALMATEC Maschinenbau GmbH is certified as a modern, quality-orientated enterprise according to DIN EN ISO 9001:2008 and 14001:2005. Before release for dispatch, any FUTUR pump has to undergo an extended final control. The performance data registered during this are archived in our records and can be read back at any time. Every individual part mentioned in the following text is identified by a number in square brackets corresponding with its item number in both the spare part list and the exploded view. The series FUTUR has specially been developed to meet...
Open the catalog to page 6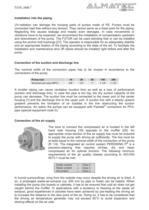
FUTU R · page 7 Installation into the piping UV-radiation can damage the housing parts of pumps made of PE. Pumps must be connected load free without any tension. They cannot serve as a fixed point for the piping. Neglecting this causes leakage and maybe even damages. In case movements or vibrations have to be expected, we recommend the installation of compensators upstream and downstream of the pump. The FUTUR can be used standing free or can be installed using the anchor bolt bushings [27]. The operator is responsible for an adequately stability and an appropriate fixation of the piping...
Open the catalog to page 7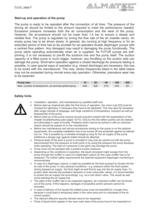
FUTU R · page 8 Start-up and operation of the pump The pump is ready to be operated after the connection of all lines. The pressure of the driving air should be limited to the amount required to meet the performance needed. Excessive pressure increases both the air consumption and the wear of the pump. However, the air-pressure should not be lower than 1,5 bar to ensure a steady and reliable flow. The pump is regulated by tuning the flow rate of the air (needle valve). An empty pump has to be driven slowly. In general, dry running at high frequency or for an extended period of time has to...
Open the catalog to page 8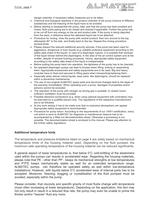
FUTU R · page 9 danger potential, if necessary safety measures are to be taken. „h Chemical and biological reactions in the product chamber of the pump (mixture of different substances) and the freezing of the liquid have to be avoided. „h Before starting to disassemble the pump, take care that the pump has been emptied and rinsed. Both ports piping are to be closed and drained if applicable. Further the pump has to be cut off from any energy on the air and product side. If the pump is being deported from the plant, a reference about the delivered liquid has to be attached. „h Procedure for...
Open the catalog to page 9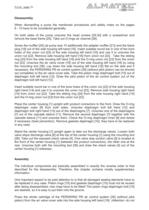
FUTU R · page 10 Disassembly When dismantling a pump the mentioned procedures and safety notes on the pages 6 - 10 have to be considered generally. On both sides of the pump unscrew the head screws [29,30] with a screwdriver and remove the base frame [25]. Take out O-rings air channel [26]. Screw the muffler [20] (at pump size 10 additionally the adapter muffler [21]) and the black plug [18] out of the side housing left hand [16]. Insert suitable round bar in one of the bore holes of the union nut [22] of the side housing left hand [16] and use it to unscrew the union nut [22]. Remove side...
Open the catalog to page 10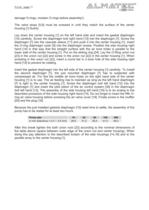
FUTU R · page 11 damage O-rings, moisten O-rings before assembly!). The valve stops [5,6] must be screwed in until they match the surface of the center housing [1] flushly. Lay down the center housing [1] on the left hand side and insert the gasket diaphragm [10] carefully. Screw the diaphragm bolt right hand [13] into the diaphragm [7]. Screw the diaphragm [7] into the cascade sleeve [11] and push it into the center housing [1]. Insert the O-ring diaphragm outer [9] into the diaphragm recess. Position the side housing right hand [14] in that way that the straight surface with the air bore...
Open the catalog to page 11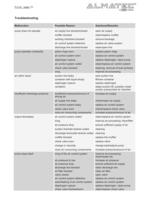
FUTU R · page 12 Troubleshooting Malfunction Possible Reason Solutions/Remarks pump does not operate air supply line blocked/closed muffler blocked working chambers blocked air control system defective discharge line blocked/closed open air supply clean/replace muffler remove blockage replace air valve system clean/open line pump operates unsteadily piston rings worn air control system worn diaphragm rupture air control system soiled check valve blocked icing replace piston rings replace air control system replace diaphragm, clean pump clean/replace air control system cleaning, removal of...
Open the catalog to page 12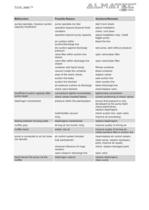
FUTU R · page 13 Malfunction Possible Reason Solutions/Remarks pumps operates, however suction capacity insufficient pump operates too fast operation beyond physical limits cavitation operation beyond pump capacity air cushion within suction/discharge line dry suction against discharge pressure valve filter within suction line closed valve filter within discharge line closed container with liquid empty vacuum inside the container wear of the check valves suction line leaky suction line blocked air pressure cushion at discharge check valve blocked start more slowly adjust installation check,...
Open the catalog to page 13All ALMATEC Maschinenbau GmbH catalogs and technical brochures
-
C- Serie
8 Pages
-
FUTUR Series
8 Pages
-
CXM Series Brochure A4
6 Pages
-
C-Series Brochure A4
6 Pages
-
Chemicor Brochure A4
8 Pages
-
Biocor Brochure A4
8 Pages
-
AHD/AHS Series Brochure A4
8 Pages
-
E-Series AODD Pumps
12 Pages
-
Almatec brochure
16 Pages
-
F-SERIES
16 Pages
-
CX
12 Pages
-
AD 6
8 Pages
-
AH
20 Pages
-
CHEMICOR
20 Pages
-
A-SERIE
28 Pages
-
E-SERIES
12 Pages
-
Pumps for low to medium duty
1 Pages
-
Decontamination-Sheet
1 Pages
Archived catalogs
-
Almatec Market Brochure
8 Pages