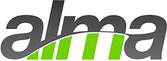

Catalog excerpts
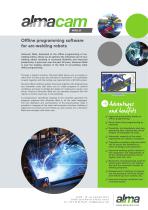
Offline programming software for arc-welding robots Almacam Weld, dedicated to the offline programming of arcwelding robots, allows you to optimize the utilization rate of your welding robots resulting in increased flexibility and improved productivity. A precursor over the past 20 years, Almacam Weld is now the leading solution in the field of arc-welding robot offline programming. Through a graphic interface, Almacam Weld allows you to program a robot from a virtual scene and simulate its movements. The assemblies to weld, together with the tooling, are imported from a 3D CAD system. Almacam Weld combines welder know-how together with programming and simulation tools that allow you to create programs in optimal conditions, and even to validate the design of a tooling or to study a cell set-up. Thanks to Almacam Weld you can generate programs that will require no further touch-ups in the workshop. A post-processor specifically adapted to the controller generates the programs prepared with Almacam Weld in all the robot languages. The cell calibration and customization of the post-processor make it possible to integrate all the robot self-correction functions (shifting of trajectories via sensing or joint follow-up, laser camera, etc.). Almacam Weld also manages multi-robot cells. Improved productivity thanks to offline programming. Much faster than programming by teaching. Possibility to immediately start programming after creating the virtual models of assemblies to weld. Automatic research of the robot trajectories for collision avoidance. Complete simulation with the whole cell to ensure the feasibility in terms of design and production. Improved welding quality thanks to the integration and repeatability of all the welding parameters (torch angles, stick out, etc.) Reduction of programming cycle for similar parts thanks to the duplication and the automatic transfer of welding programs. Management of shifting of trajectories via sensing of wire and nozzle, joint follow-up, laser camera, etc. Improved working conditions and increased safety.
Open the catalog to page 1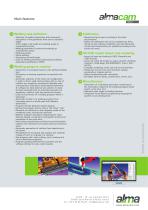
Main features WELD Welding task definition • Selection of welding trajectories with automactic recognition of the geoemetry from part or assembly edges. • Torch angles, wire length and welding speed at characteristic points. • Welding parameters (current and weaving) at characteristic points. • Multi-pass seams. • Stitch welding. • Sequencing of weld beads. • Copy of welding parameters (reproducing welding parameters specification: WPS). • Repositioning the part according to the robot requirements. • Robot cell calibration task to be completed by Alma during on-site software installation...
Open the catalog to page 2All ALMA catalogs and technical brochures
-
Almaquote product brochure
2 Pages
-
Almacam Routing Brochure
2 Pages
-
Product Flyer almaCube
1 Pages