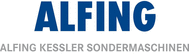
Catalog excerpts
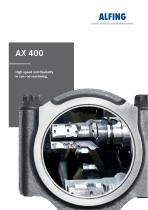
AX 400 High speed and flexibility in con rod machining.
Open the catalog to page 1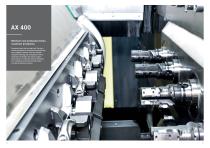
AX 400 Minimum non-productive times maximum production. Extremely short chip-to-chip time: The short travels guarantee an extremely low positioning time. Together with the main time parallel component loading and unloading as well as the quick tool change, this means unique peak values for a machine with the flexibility of a machining center and the high output of a special purpose machine.
Open the catalog to page 2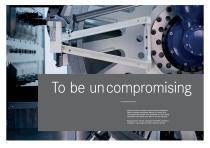
To be uncompromising means to create a customer-oriented concept leaving the limits of existing technologies behind. As a result, this uncompromising attitude is the foundation of a new, highly specialized and modular generation of con rod machines. High production volume. Consequent flexibility. Individual scalability. Low change-over times. Highest precision.
Open the catalog to page 3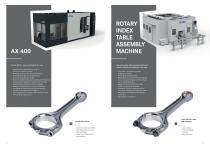
ROTARY INDEX TABLE ASSEMBLY MACHINE AX 400 The AX 400 for rough machining of con rods. The rotary index table assembly machine for fracture splitting and assembly of con rods. · Productive as a special purpose machine, flexible as a machining center. · Machining of up to 4 con rods simultaneously · Extremely short chip-to-chip time thanks to main time-parallel tool change · Main time-parallel loading and unloading of components · Loading robot integrated in machine control, thereby simple operation without any robot knowledge · Ergonomic loading station for quick and fool-proof tool change,...
Open the catalog to page 4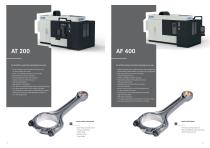
The AT 200 for semi-finish machining of con rods. The AF 400 machine for finish machining of con rods. · Up to 4 fixtures can be mounted simultaneously for short change-over times · Up to 2 turret heads with each 4, 6 or 8 tools · Extremely short chip-to-chip time · No chip problems at the tool interface thanks to the use of the tool turret · High thermal stability · High operator convenience · Very good accessibility for maintenance and tool change · Low space requirement in floor space and height · Very versatile: as variant with Y-stroke 630 mm a highly productive and process-safe...
Open the catalog to page 5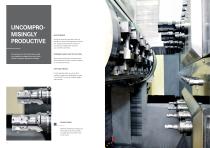
UNCOMPROMISINGLY PRODUCTIVE Two spindle rows with alternately acting main spindles arranged above each other enable a maintime-parallel tool change. MAIN SPINDLES During the machining process of the one spindle row, tools are changed at the second row. Thanks to this minimum number of cost-intensive spindles the maximum cost / benefit is achieved. EXTREMELY SHORT CHIP-TO-CHIP TIME Short travels guarantee an extremely short positioning time and thus a drastic reduction of non-productive times. STIFF AND PRECISE Usual projecting quills as used in other machine concepts are deliberately not...
Open the catalog to page 6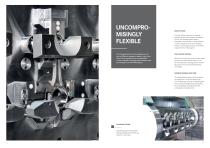
UNCOMPROMISINGLY FLEXIBLE The clamping fixture can be changed over to new or different component types in very short time. This is possible due to a combination of semi-automatic clamping plate change as well as exchange of tool and NC program. The clamping fixture with twofold bearing, swiveling around the A-axis, moves in Y- andZ-axis. BASIC FIXTURE The basic fixture comprises the clamping cylinders as well as the clamped/unclamped control. The clamping cylinder itself is integrated in the basic fixture, being reflected in a lower weight and lower cost. Clamping sequence and clamping...
Open the catalog to page 7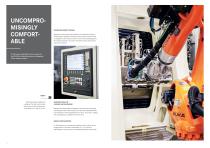
UNCOMPROMISINGLY COMFORTABLE In the future-orientated control concept of the AX 400, all robot functions are integrated in the machine control. INTEGRATED ROBOT CONTROL Whereas in usual systems the operation of robot and machine is realized with 2 separate controls, the robot control of the AX 400 is integrated in the machine control. From the NC operating panel, the machine operator can control all robot functions and read all relevant information. Maintime-parallel loading and MAINTIME-PARALLEL unloading: The fully synchronized LOADING AND UNLOADING robot is part of the machine axes and...
Open the catalog to page 8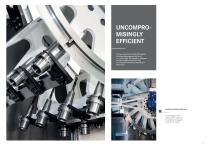
UNCOMPRO MISINGLY EFFICIENT The tool magazine of the AX 400 consists of a drum-type magazine with in all 16 x 4 tool seats. The capacity is designed to make available several tool sets for component machining, depending on the process. MINIMUM CHANGE-OVER TIME The tool magazine with a capacity of 16 x 4 tools can be completely re-equipped in less than 10 minutes.
Open the catalog to page 9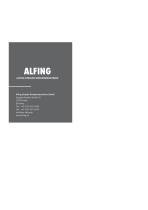
Alfing Kessler Sondermaschinen GmbH Auguste-Kessler-StraRe 20 73433 Aalen Germany Fon: +49 7361 501-6340 Fax: +49 7361 501-6533 info@aks.alfing.de www.alfing.de
Open the catalog to page 10All Alfing Kessler Sondermaschinen GmbH catalogs and technical brochures
-
FIXTURE SPINDLE TECHNOLOGY
40 Pages
-
HANDHELD NUTRUNNER TECHNOLOGY
48 Pages
-
AM Manufacturing Module
16 Pages
-
AF 400
10 Pages
-
AT 200
10 Pages