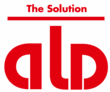
Catalog excerpts
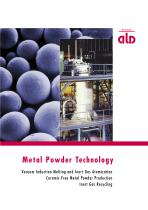
Metal Powder Technology Vacuum Induction Melting and Inert Gas Atomization Ceramic-Free Metal Powder Production Inert Gas Recycling
Open the catalog to page 1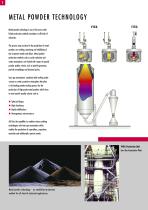
METAL POWDER TECHNOLOGY Metal powder technology is one of the most estab- lished production methods nowadays in all kinds of industries. The process steps involved in the production of metal powders are melting, atomizing and solidifying of the respective metals and alloys. Metal powder production methods such as oxide reduction and water atomization, are limited with respect to special powder quality criteria, such as particle geometry, particle morphology and chemical purity. Inert gas atomization, combined with melting under vacuum or under protective atmosphere therefore is the leading...
Open the catalog to page 2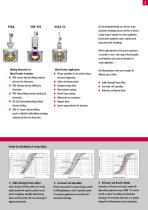
ALD has developed through over 30 years in gas atomization technology process know-how to atomize a broad range of materials for various applications. Each particular application needs a special particle shape and powder morphology. With the right adjustment of the process parameters it is possible to cover a wide range of desired powder size distributions and to meet the demands for various applications. Melting Alternatives in Metal Powder Applications: The following pictures show some examples for n Ni-base superalloys for the aviation industry Metal Powder Production n VIGA: Vacuum...
Open the catalog to page 3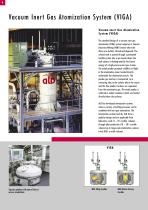
Vacuum Inert Gas Atomization System (VIGA) Vacuum Inert Gas Atomization System (VIGA) The standard design of a vacuum inert gas atomization (VIGA) system comprises a Vacuum Induction Melting (VIM) furnace where the alloys are melted, refined and degassed. The refined melt is poured through a preheated tundish system into a gas nozzle where the melt stream is disintegrated by the kinetic energy of a high pressure inert gas stream. The metal powder produced solidifies in flight in the atomization tower located directly underneath the atomization nozzle. The powder gas mixture is transported...
Open the catalog to page 4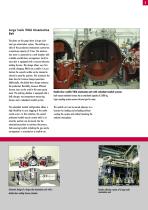
Large Scale VIGA Atomization Unit The photo on this page shows a large scale inert gas atomization system. The melting crucible of this production atomization system has a maximum capacity of 2 tons. The atomization tower is connected to a melt chamber with a double-crucible door arrangement. Each furnace door is equipped with a vacuum induction melting furnace. This design allows very fast crucible changing. While one crucible is in production the second crucible can be cleaned or relined in stand-by position. This minimizes the down time for furnace change operations. Additionally, the...
Open the catalog to page 5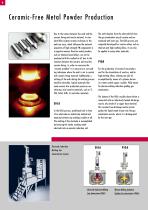
Ceramic-Free Metal Powder Production Due to the contact between the melt and the ceramic lining and nozzle material, in standard VIGA systems ceramic inclusions in the melt can occur, which influence the material properties of high-strength PM-components in a negative manner. Reactive metal powders, such as titanium based alloys, can not be produced with this method at all, due to the reactions between the reactive melt and the ceramic lining. In order to overcome the “ceramic problem” it is necessary to use melting techniques where the melt is not in contact with ceramic lining material....
Open the catalog to page 6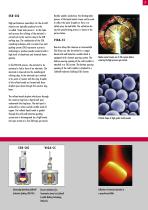
ESR-CIG High performance superalloys for the aircraft industry are typically produced via the so-called “triple melt process”. In the triple melt process the refining of the material is carried out by the reactive slag in the ESR melting step. The combination of the ESR remelting technique with a ceramic-free melt guiding system (CIG) represents a process technology to produce powder material with a high level of cleanliness and chemical homogeneity. In the ESR-CIG process, the material to be atomized is fed in form of an electrode. The electrode is lowered into the metallurgical refining...
Open the catalog to page 7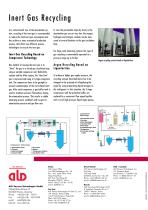
Inert Gas Recycling At a certain batch size of the atomization system, recycling of the inert gas is recommended, to reduce the total inert gas consumption and thus achieve a more economical production process. ALD offers two different process technologies to recycle the inert gas. In case the permissible impurity levels in the atomization gas are set very low, the oxygen, hydrogen and nitrogen contents can be measured at several locations in the gas circulation loop. For large-scale atomizing systems this type of gas recycling is economically operated in a pressure range up to 50 bar....
Open the catalog to page 8All ALD catalogs and technical brochures
-
Plasma Arc Melting
4 Pages
-
Laboratory Remelting Systems
6 Pages
-
Electron Beam Melting (EB)
6 Pages
-
Vacuum Arc Remelting (VAR
8 Pages
-
ASPN Plasma Nitriding
6 Pages
-
Metal Additive Manufacturing
4 Pages
-
Vacuum Turbine Blade Coating
6 Pages
-
LPC Engineering Service
2 Pages
-
Vacuum freeze drying
6 Pages
-
Vacuum Arc Remelting (VAR)
6 Pages
-
Electroslag Remelting (ESR)
8 Pages
-
Electron Beam Melting (EB)
6 Pages
-
Vacuum Sintering
10 Pages
-
Blade Runner™
2 Pages
-
MonoTherm
10 Pages
-
DualTherm
2 Pages
-
ModulTherm 2.0
10 Pages
-
SynroTherm
10 Pages