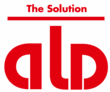
Catalog excerpts
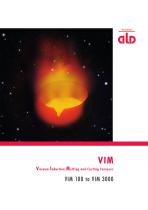
Vacuum Induction Melting and Casting Furnaces
Open the catalog to page 1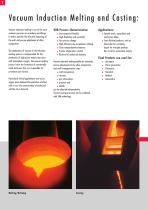
Vacuum Induction Melting and Casting: Vacuum induction melting is one of the most common processes in secondary metallurgy. It makes possible the effective degassing of the melt and precise adjustment of alloy composition. The application of vacuum in the induction melting process is indispensable for the production of high purity metals that react with atmospheric oxygen. The vacuum melting process limits the formation of non-metallic oxide inclusions that are responsible for premature part failure. Particularly critical applications such as jet engine parts demand the production of alloys...
Open the catalog to page 2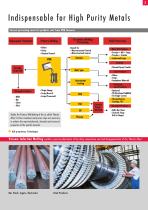
Indispensable for High Purity Metals Current processing route for products cast from VIM furnaces ubsequent Treati Primary Meltin • Chemical Control • Virgin Charge Beside the Primary VIM Melting of the so called "Master Alloy" further treatment and process steps are necessary to achieve the required physical, chemical and structural properties of the specific material. Macrostructural Control Microstructural Control Melt Spin Near-Net Shapes • Isothermal Forge • Thermal Spray Powder Cast Products • Amorphous Material • DS-Directional Solidified • SX-Single Crystal • Thermal Barrier Wrought...
Open the catalog to page 3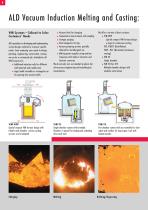
ALD Vacuum Induction Melting and Casting: Vacuum locks for charging Temperature measurement and sampling Inertgas purging Electromagnetic stirring Vacuum-pumping systems specially tailored for metallurgical use Melting power-supplies using medium frequency with modern transistor and thyristor converter We do not only turn out standard products but solve process-engineering and metallurgical requirements. We offer a variety of basic versions: VIM-VIDP Special compact VIM furnace design Ingot or continuous casting VID, VIDEST (Destillation) VIDP - HCC (Horizontal continuous casting) VIM V2...
Open the catalog to page 4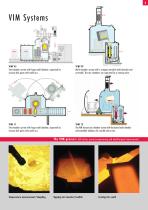
VIM V5 Two-chamber system with large mold chamber, separated by vacuum-lock gates with mold cars. VIM V9 Multi-chamber system with a compact movable mold chamber and turntable. The two chambers are separated by a casting valve. VIM 11 Two-chamber system with large mold chamber, separated by vacuum-lock gates with mold cars. VIM 12 The VIM furnace one chamber system with horizontal melt chamber and moveable sidedoors for crucible coil service. The VIM process: ALD solves process-engineering and metallurgical requirements. Temperature measurement/Sampling Tapping into launder/tundish Casting...
Open the catalog to page 5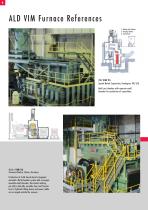
1 Melting/Cast Chamber 2 Charging Chamber 3 Control Room 3 25t VIM V5 Special Metals Corporation, Huntington, WV, USA Melt/cast chamber with separate mold chamber for production of superalloys. 4/6 t VIM V6 Vacuumschmelze, Hanau, Germany Production of Fe-Ni based electric/magnetic materials. Multi-chamber system with a compact movable mold chamber. Horizontal melting pot with a laterally movable door and furnace insert. Hydraulic tilting device and power cables are arranged outside the vacuum.
Open the catalog to page 6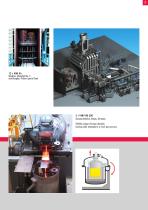
12 t VIM V6 Baoshan, Shanghai No. 5 and Dongbei, Fushun Special Steel 3 t VIM VID 300 Vacuumschmelze, Hanau, Germany Tiltable compact furnace chamber. Casting under atmosphere or inert gas pressure.
Open the catalog to page 7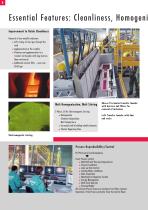
Essential Features: Cleanliness, Homogeni Improvement in Oxide Cleanliness Removal of non-metallic inclusions ■ Soft rinsing of inert gas through the transfer hot launder with slag barriers ■ Additional ceramic filter - pore size Melt Homogenization, Melt Stirring Chemical Composition Melt Temperature ■ Increased yield of adding volatile elements ■ Shorter Degassing Time Above: Pre-heated transfer launder with barriers and filters for Left: Transfer launder with dam Electromagnetic stirring Process Reproducibility/Control Exact Process Control ■ Melt Bath and Pouring Temperatures ■ Leak-up...
Open the catalog to page 8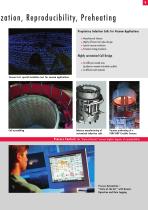
zation, Reproducibility, Preheating Proprietary Induction Coils for Vacuum Applications Manufactured inhouse Highly efficient and robust design Special vacuum insulation Extensive testing procedures Highly customized Coil Design for different crucible sizes (prefired or rammed or bricked crucible) to different melt materials Corona test: special insulation test for vacuum applications Coil assembling Inhouse manufacturing of customized induction coils Vacuum preheating of a VIM-VIDP Crucible Furnace Process Control: The “State - o f - t h e - Ar t” ensures highest degrees of...
Open the catalog to page 9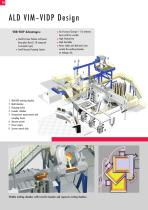
ALD VIM–VIDP Design VIM-VIDP Advantages: Small Furnace Volume and lowest Desorption Rate (1:10 compared to chamber type) Small Vacuum Pumping System Fast Furnace Change < 1 hr between heats with hot crucible High Productivity High Flexibility Power Cables and Hydraulic Lines outside the melting chamber, no leakage risk 3 5 VIM-VIDP melting chamber Mold chamber Charging device Launder chamber Temperature measurement and sampling device 6 Vacuum system 7 Power supply 8 System control desk Tiltable melting chamber with transfer launder and separate casting chamber
Open the catalog to page 10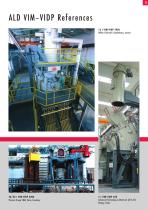
ALD VIM–VIDP References 16 t VIM-VIDP 2000 Böhler Edelstahl, Kapfenberg, Austria 20/30 t VIM-VIDP 3000 Thyssen Krupp VDM, Unna, Germany 2 t VIM-VIDP 400 Advanced Technology & Materials (AT & M) Beijing, China
Open the catalog to page 11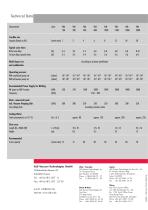
Technical Data Characteristic Crucible size Capacity (based on Ni) Typical cycle times Ni-Co base alloy Fe base alloys/special steels According to customer specification Mold/Ingot size and combination Operating pressure With mechanical pump set With oil booster pump set (mbar) (mbar) Recommanded Power Supply for Melting MF power at 600 V output Frequency Electr. connected Loads incl. Vacuum Pumping Unit Line-voltage data 250 250 250 According customer mains Cooling Water Total consumption (∆t=10 °C) Floor area Length (L) x Width (W) Height Recommended Crane capacity USA / Canada ALD Vacuum...
Open the catalog to page 12All ALD catalogs and technical brochures
-
Plasma Arc Melting
4 Pages
-
Laboratory Remelting Systems
6 Pages
-
Electron Beam Melting (EB)
6 Pages
-
Vacuum Arc Remelting (VAR
8 Pages
-
ASPN Plasma Nitriding
6 Pages
-
Metal Additive Manufacturing
4 Pages
-
Vacuum Turbine Blade Coating
6 Pages
-
LPC Engineering Service
2 Pages
-
Vacuum freeze drying
6 Pages
-
Vacuum Arc Remelting (VAR)
6 Pages
-
Electroslag Remelting (ESR)
8 Pages
-
Electron Beam Melting (EB)
6 Pages
-
Vacuum Sintering
10 Pages
-
Blade Runner™
2 Pages
-
MonoTherm
10 Pages
-
DualTherm
2 Pages
-
ModulTherm 2.0
10 Pages
-
SynroTherm
10 Pages