

Catalog excerpts
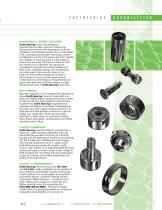
MACHINERY & TESTING FACILITIES Smith Bearing® has a fully-integrated manufacturing facility capable of producing high-precision needle roller bearings for both the Aerospace and Industrial market. Our computerized (CNC) grinding and precision machining centers, considered to be the most advanced in the industry are capable of manufacturing a wide range of products to exacting tolerances in order to meet the needs of our customers. Our advanced metallurgical department routinely verifies and tests all raw materials, plating and heat-treating processes used in the manufacturing of our products. This careful analysis and scrutiny in each phase of our procedure assures proper conformance to all Aerospace requirements and guarantees that only materials meeting our rigid standards are used in Smith Bearing® products. ENGINEERING Extensive experience in our engineering department allows Smith Bearing® to work closely with end-users and OEMS (original equipment manufactures) in order to offer the best solution for their bearing requirements. Smith Bearing® engineers have extensive knowledge of available metallurgies so that they may offer customers their experience to determine the best suitable material for a special design and application. Smith manufactures bearings in a wide range of materials including high-carbon alloy steels, stainless steels, tool steels, and other exotic alloys. CUSTOM ASSEMBLIES Smith Bearing® has the ability to manufacture a variety of custom bearing assemblies. Typically this entails the precision machining of a bearing housing and the assembly of needle or ball bearings into the housing. By controlling the entire design and manufacturing process of a custom order, Smith Bearing® guarantees the quality, performance, and delivery of an assembly. Smith Bearing® performs all aspects of such projects from design to finish including the machining process, applications of special coatings and plating, assembling and testing of the final product. QUALITY & DEPENDABILITY Smith Bearing® has received both ISO 9001 and AS 9100 quality registrations in recognition of our continued commitment to world-class quality control systems. Our quality system is recognized by General Electric, Lockheed, Boeing Aircraft Corporation, British Aerospace, as well as many other military and aerospace companies. Our Military bearings meet the requirements of Mil-B-3990 (SAE AS 39901). This level of quality certifications and approvals assures our customers unequaled dependability of our products.
Open the catalog to page 1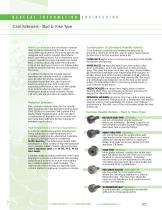
Cam Followers – Stud & Yoke Type SMITH Cam Followers are anti-friction needle roller bearings developed for use in cam or track roller applications. They were specifically designed and built to handle intermittent shock and heavy loads. Full compliment (noncaged) needle bearings maximize the radial load carrying capability while the soft inner core of the stud gives these cam followers the ability to absorb extreme shock loads without fracturing. In addition to standard models, special bearings are manufactured to customer specification for unique applications. It is often found that the...
Open the catalog to page 2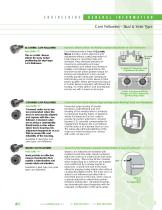
Cam Followers – Stud & Yoke Type Eccentric Sleeves Allow for Radial Location Adjustment of Cam Followers Cam Followers with a Press Fit Eccentric Sleeve provide correct alignment and adjustment without costly preparation of close tolerance mounting holes and members. They eliminate problems of clearances, preloading and wear compensation and assure load sharing in multiple cam follower applications. The hex-drive socket allows positive torque for locking and adjustment. A lock nut will normally provide adequate clamping to hold bearing and eccentric sleeve in their proper position. When...
Open the catalog to page 3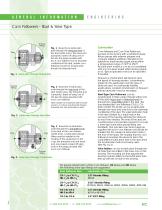
Cam Followers - Stud & Yoke Type Grease Fitting Fig. 1 shows the re-lubrication path through the threaded-end of the stud (white area). The head-end is properly closed off using one of the two the plugs provided with each cam follower. Due to diameter constraints of the stud, smaller cam followers cannot be re-lubricated though the threaded-end. Fig. 2 shows the re-lubrication path through the head-end of the stud (white area). The threaded-end is properly closed off using one of the two the plugs provided with each cam follower. Note: Smaller cam followers with hex-drive socket can only be...
Open the catalog to page 4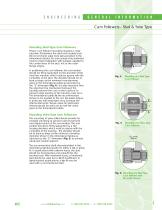
Cam Followers – Stud & Yoke Type Mounting Stud-Type Cam Followers Proper cam follower mounting requires a close precision fit between the stud and housing bore. We recommend using bore sizes provided in the dimensional tables. An arbor press is the preferred means of stud installation with pressure applied to the central area of the stud, not to the outer flange edges. In positioning the cam follower, the end washer should be firmly supported by the shoulder of the machine member, which must be square with the centerline of the stud. The shoulder should be at least as large as the minimum...
Open the catalog to page 5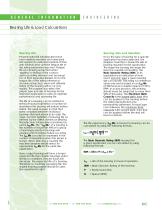
Bearing Life & Load Calculations Bearing Life Properly selected bearings that have been suitably mounted and lubricated will operate for extended periods of time with minimal wear until the fatigue life of the rolling elements is reached. Fatigue life of a bearing is reached when "spalling" or flaking of the contact surfaces (rolling element and raceway) occur from repeated stresses. Once the fatigue life of the rolling element or raceway is reached, wear and ultimate failure of the bearing will occur very rapidly. The purpose is to select the proper type and size of bearing for the...
Open the catalog to page 6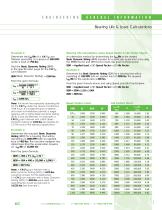
GENERAL Bearing Life & Load Calculations Example 1: Determine the L10 life of a CR-7/8 cam follower operating at a speed of 500 RPM under a load of 750 lbs: Find the Basic Dynamic Rating (BDR) in the specification page for the CR-7/8 cam follower: BDR (Basic Dynamic Rating) = 2140 lbs From the given formula: Note: This shows the expected operating life for the CR-7/8 under the above conditions is 1098 hours, If a longer life span is desired and room for installation permits, a larger bearing with a higher Basic Dynamic Rating (BDR) could be selected, For example: a CR-11/4 cam follower with...
Open the catalog to page 7All ACCURATE BUSHING catalogs and technical brochures
-
DRILL JIG BUSHINGS
1 Pages
-
Aerospace Bearings
2 Pages
-
Smith-Trax
1 Pages
-
Catalog 2014
116 Pages
-
SMITH BEARING ® Product Catalog
115 Pages
Archived catalogs
-
Drill Jig Intro
1 Pages
-
Aerospace Intro
2 Pages
-
SMITH-TRAX Intro
1 Pages
-
Engineering Capabilities
10 Pages
-
Complete catalogue
115 Pages