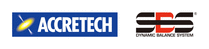

Catalog excerpts
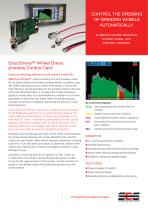
CONTROL THE DRESSING OF GRINDING WHEELS AUTOMATICALLY. ELIMINATE EXCESS GRINDING. EXTEND WHEEL LIFE. PREVENT CRASHES. ExactDress™ Wheel Dress process Control Card Improve dressing efficiency and extend wheel life. SBS ExactDress™ reduces dressing time and increases wheel life for both profiled and standard grinding wheels. ExactDress uses SBS AEMS proprietary acoustic sensor technology to monitor the high requency signals generated on the grinding machine structure f during the dressing process. It compares the current AE process signal of a wheel dress to a stored Reference waveform of a known good dress to determine and report when the dressing process has been successfully completed, maximizing the efficiency of the dressing process. Setup couldn’t be easier. Simply dress a wheel to teach the system the AE Reference waveform of a successful dressing process. The s ystem maps the entire duration of the process and breaks it into time slices or “zones,” indicated by a bar graph on screen. uring D operation, the system displays which (if any) of the zones in the dressing process are not complete, and informs the CNC control when the entire dress process has completed successfully. ExactDress also includes gap and crash control. Initial contact between the wheel and the dressing tool can be detected so the machine c ontrol can stop wheel in-feed without operator inter ention, reducing v cycle time. It can also detect and report an bnormal contact within a milliseconds, allowing the in-feed to be stopped, avoiding a crash, damage or injury. ExactDress monitoring permits the operator or CNC control to (1) determine if the wheel is being dressed fully across its width, (2) control the aggressiveness of the process, and (3) maintain the quality of the dressed wheel while conserving process time and wheel material. DC or AC Power Options: Green Zones exceeding the Zone Minimum limit are complete. Yellow Borderline zones nearing Out of Tolerance. Gray Learned Reference waveform shown in background. Red below the Zone Minimum limit are incomZones plete or defective. Blue Indicates zones which are below the Ignore Level. BENEFITS: Cut cycle time and increase productivity Eliminate excess dressing Automate dressing in-feed to prevent crashes and damage Improve wheel surface quality with precise monitoring Extend life of dressers and spindle bearings FEATURES: Enhances features of the AEMS Backed by world-class, worldwide SBS customer service Productivity through Precision Eine Produk
Open the catalog to page 1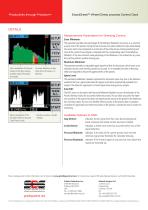
Productivity through Precision™ ExactDress™ Wheel Dress process Control Card DETAILS Measurement Parameters for Dressing Control Zone Minimum: This parameter specifies what percentage of the Reference Waveform must occur as a minimum at each zone of the process. During the teach process, the system divides the cycle automatically into zones. Each zone corresponds to a time slice of the entire process. During monitoring each zone of the current Process Signal is compared with the corresponding value of the Reference Waveform. If the zone minimum value percentage of the Reference is not...
Open the catalog to page 2All Accretech SBS catalogs and technical brochures
-
Product Catalog
53 Pages
Archived catalogs
-
SBS Product
6 Pages
-
SB5523 ExactDress
2 Pages
-
SB5522 AEMS
2 Pages
-
SB5500
2 Pages
-
SB-55xx
2 Pages
-
AE-1000
2 Pages
-
SBS-500 Brochure
2 Pages
-
Control Grinding
2 Pages
-
Product catalog
65 Pages