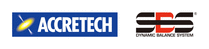

Catalog excerpts
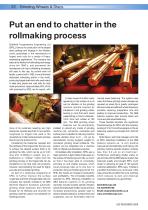
GSF GRIND WHEELS & DISCS 20-25:GSF GRIND WHEELS & DISCS 36-41 22 Grinding Wheels & Discs Put an end to chatter in the rollmaking process Sheffield Forgemasters Engineering Ltd (SFEL), famous for production of the largest steel castings and forgings in the Western world, specialises in the manufacture of forged work rolls for a variety of heavy engineering applications. The company has been at the forefront of rollmaking technology since the 1860’s, and pioneered the development of many rollmaking processes still used to this day. Its current work roll facility, custom built in 1992, is one of the best dedicated rollmaking plants in the world, producing forged steel work rolls used mainly in steel strip plants and cold mills for strip metal production. Approximately 90% of the rolls produced by SFEL are for export, with many of its customers requiring very high tolerances, typically less than 0.5 µm surface roughness on forged rolls used in the manufacture of strip metal products and less than 0.2 µm for aluminium foil. Considering the tolerances required and the hardness of the forged rolls, the only way to achieve the desired surface finish is by grinding the rolls, which can be up to 5.3m long and 12,000kg in weight. Any imperfections or “chatter” marks from the grinding process on the forged rolls can be transferred to the final strip mill products, however, demonstrating the need for highly accurate and consistent grinding. As part of a continuous programme at SFEL to further improve the surface roughness and finish of forged steel rolls, the company has recently invested in six SBS (Schmitt Balance Systems) automatic grinding wheel balancers from Schmitt Europe for its Herkules and Churchill roll grinding machines used in the hardened roll finishing process. A major cause of chatter marks appearing on the surface of a roll can be vibration on the grinding machine spindle induced by imbalance in the grinding wheel, bearing in mind that each wheel weighs 80 kg, is 73cm in diameter, 10cm thick and rotates at 700 rpm. The SBS grinding wheel balancer can be permanently installed on almost any model of grinding machine (roll, cylindrical, centreless and surface) and is capable of reducing machine spindle vibration down to 0.1 – 0.2 µm by automatically moving tungsten weights to counteract grinding wheel imbalance. The system can be integrated into a machine CNC or offered as a standalone solution. Immediately after installation, SFEL saw a major reduction in light chatter marks seen on the surface of finished ground rolls, so much so that it has been able to completely eliminate an anti-chatter process, which could previously take up to one hour of production time per finished ground roll. For SFEL this means an increase in productivity and profitability. The immediate benefits reported by SFEL following installation of SBS balance systems to its grinding machines include lowered spindle vibration (which eliminates light chatter marks and thus increases productivity), greater ease to achieve desired tolerance, surface finish and roughness, and an eliminated need for manual wheel balancing. The systems also mean that fewer grinding wheel changes are required as wheel life is greatly prolonged. More accurate and efficient wheel dressing is possible, reducing preparation time and leading to improved productivity. The SBS balance systems also provide faster and more accurate wheel balancing. These benefits translate into significant financial savings for SFEL with the company looking at 12 to 18 months payback on the six balancing systems purchased from Schmitt Europe. Robin Bown, technical manager work rolls at SFEL described installation of the SBS balance systems as, “a very positive improvement and definitely worth doing, with grinding machine spindle vibration routinely less than 0.2 µm on all machines”. Furthermore, eliminating chatter marks on ground rolls with the SBS balance system has improved quality and brought SFEL much closer to achieving its goal of 100 percent customer satisfaction. SFEL says, “Chatter is a problem that follows you round and, in this case, prevention is better than cure. Anything which reduces re-work and improves customer satisfaction is a good thing”. Schmitt Europe Ltd Tel: 02476 697192 Email: enquiries@schmitt.co.uk www.schmitteurope.com
Open the catalog to page 1All Accretech SBS catalogs and technical brochures
-
Product Catalog
53 Pages
Archived catalogs
-
ExactDress Card
2 Pages
-
SBS Product
6 Pages
-
SB5523 ExactDress
2 Pages
-
SB5522 AEMS
2 Pages
-
SB5500
2 Pages
-
SB-55xx
2 Pages
-
AE-1000
2 Pages
-
SBS-500 Brochure
2 Pages
-
Control Grinding
2 Pages
-
Product catalog
65 Pages