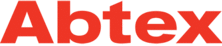
Catalog excerpts
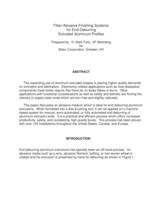
Prepared by: D. Mark Fultz, VP MarketingforAbtex Corporation, Dresden, NY ABSTRACT The expanding use of aluminum extruded shapes is placing higher quality demandson extruders and fabricators. Electronics related applications such as heat dissipation components (heat sinks) require that there be no loose flakes or burrs. Other applications with functional considerations as well as safety and esthetic are forcing the industry to supply sawn ends which are burr free and slightly radiused. This paper discusses an abrasive medium which is ideal for end deburring aluminumextrusions. When formatted into a disc brushing tool, it can be applied on a machine based system for manual, semi-automated, or fully automated end deburring of aluminum extrusion ends. It is a practical and efficient process which offers increased productivity, safety, and consistently high quality levels. This process has been proven with over 100 installations throughout the United States, Canada, and Europe. INTRODUCTION End deburring aluminum extrusions has typically been an off-hand process. Anabrasive media such as a wire, abrasive filament, buffing, or non-woven wheel is rotated and the extrusion is presented by hand for deburring as shown in Figure 1. >
Open the catalog to page 1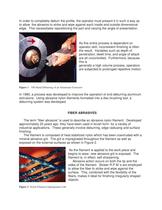
Figure 1 Off-Hand Deburring of an Aluminum Extrusion > Figure 2 Nylon Filament Impregnated with >
Open the catalog to page 2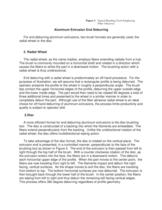
Figure 3 Typical Brushing Tools Employing Fiber Abrasives Aluminum Extrusion End Deburring For end deburring aluminum extrusions, two brush formats are generally used; theradial wheel or the disc. 2.Disc 2. Radial Wheel A more efficient format for end deburring aluminum extrusions is the disc brushingtool. The disc is constructed of a backing into which the filaments are embedded. The fibers extend perpendicularly from the backing. Unlike the unidirectional rotation of the radial wheel, the disc offers multidirectional wiping action. To take advantage of the disc format, the disc is rotated...
Open the catalog to page 4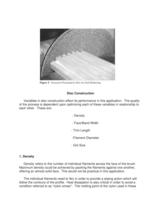
Figure 4 Extrusion Presented to Disc for End Deburring 1. Density Disc Construction Density refers to the number of individual filaments across the face of the brush.Maximum density could be achieved by packing the filaments against one another, offering an almost solid face. This would not be practical in this application. The individual filaments need to flex in order to provide a wiping action which willfollow the contours of the profile. Heat dissipation is also critical in order to avoid a condition referred to as nylon smearӔ. The melting point of the nylon used in these Variables in...
Open the catalog to page 5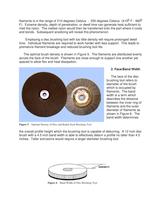
Figure 5 Optimal Density of Disc and Radial Style Brushing Tool > Figure 6 Band Width of Disc Brushing Tool >
Open the catalog to page 6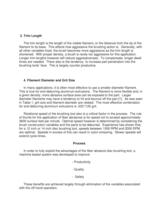
3. Trim Length Process The trim length is the length of the visible filament, or the distance from the tip of thefilament to its base. This affects how aggressive the brushing action is. Generally, with all other variables fixed, the brush becomes more aggressive as the trim length is shortened. With proper density, a brush is rarely too aggressive for this application. Longer trim lengths however will reduce aggressiveness. To compensate, longer dwell times are needed. There also is the tendency to increase part penetration into the brushing tools face. This is largely counter productive....
Open the catalog to page 7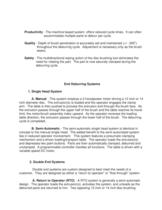
Productivity - The machine based system offers reduced cycle times. It can often accommodate multiple parts to deburr per cycle. Quality - Depth of brush penetration is accurately set and maintained (+/- .005) throughout the deburring cycle. Adjustment is necessary only as the brush wears. Safety - The multidirectional wiping action of the disc brushing tool eliminates the need for rotating the part. The part is now securely clamped during the deburring cycle. End Deburring Systems1. Single Head SystemA. Manual 2. Double End Systems B. Semi-Automatic - The semi-automatic single head system...
Open the catalog to page 8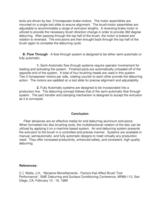
B. Flow Through - A flow through system is designed to be either semi-automatic orfully automatic. tools are driven by two, 3 horsepower brake motors. The motor assemblies aremounted on a single tool slide to ensure alignment. The brush/motor assemblies are adjustable to accommodate a range of extrusion lengths. A reversing brake motor is utilized to provide the necessary brush direction change in order to provide 360 degree deburring. After passing through the top half of the brush, the motor is braked and rotation is reversed. The extrusions are then brought back through the top half of...
Open the catalog to page 9All Abtex catalogs and technical brochures
-
Tri-Ten Series
2 Pages
-
Dust collector
4 Pages
-
Abtex Turnamat
2 Pages
-
Capabilities
4 Pages
-
Robotic Deburring
1 Pages
-
End Deburring Systems
4 Pages
-
catalog
16 Pages
-
Tri-Ten Series
2 Pages
-
Tri-Ten U-Series
2 Pages
Archived catalogs
-
Focus on: working with metal
2 Pages
-
Artifex Technology
2 Pages
-
Artifex-XC
1 Pages
-
Artifex-Z
1 Pages
-
Artifex-R/N
2 Pages
-
Artifex-P/P-Plus
2 Pages
-
Artifex-E
2 Pages
-
Artifex-D
2 Pages
-
Artifex-A
2 Pages
-
Brush deburring brochure
13 Pages