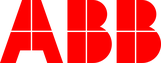
Group: ABB
Catalog excerpts
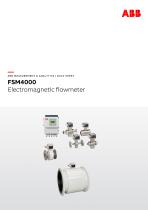
—ME ASURE ME NT & AN AL YT ICS | D AT A SHE ET ABB FSM4000 Electromagnetic flowmeter
Open the catalog to page 1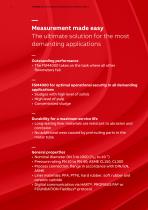
— Measurement made easy The ultimate solution for the most demanding applications — Outstanding performance • The FSM4000 takes on the task where all other flowmeters fail. — FSM4000 for optimal operational security in all demanding applications • Sludges with high level of solids • High level of pulp • Concentrated sludge — Durability for a maximum service life • Long-lasting liner materials are resistant to abrasion and corrosion • No additional wear caused by protruding parts in the meter tube — General properties • Nominal diameter DN 3 to 1000 (¹⁄₁₀ to 40 ”) • Pressure rating PN 10 to...
Open the catalog to page 2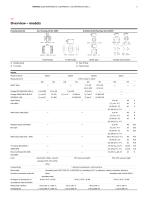
— Overview – models Housing material Fixed Flange Stainless Steel Housing, Series 2000 Fixed Flange Wafer type Variable Connections Sensor Model number Measured error Pipe fitting Wafer type Hard/soft rubber, ceramic ASME BPE External thread ISO 228 / DIN 2999 Liner carbide, PTFE, PFA, ETFE, other Conductivity Electrodes Process connection material ≥ 20 µS/cm (optional ≥ 5/0.5 µS/cm) Stainless steel 1.4571 (316 Ti), 1.4539 (904 L), Hastelloy B-3/C-4, platinum-iridium, tantalum, titanium Steel, stainless steel IP degree of protection in
Open the catalog to page 3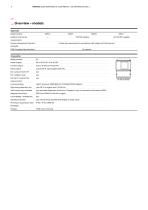
— … Overview – models Approvals Model number requirements Pressure Equipment Directive Conformity assessment in accordance with category III, fluid group 1 Transmitter Model number Power supply Current output Pulse output Forward / reverse flow measurement Communication HART® protocol, PROFIBUS PA®, FOUNDATION Fieldbus® Pipe empty detection std. Self-monitoring, extended yes, extended diagnostic functions / fingerprint only in connection with sensors SE21, diagnosis functions Local display / totalization Density correction yes, manual entry (totalize and display in mass units) IP rating in...
Open the catalog to page 4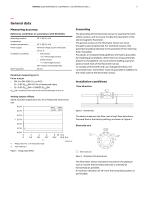
— General data Measuring accuracy Reference conditions in accordance with EN 29104 The grounding of the flowmeter sensor is essential for both safety reasons, and to ensure trouble-free operation of the electromagnetic flowmeter. The ground screws on the flowmeter sensor are to be brought to ground potential. For technical reasons, this potential should be identical to the potential of the metering fluid, if possible. For plastic or insulated lined pipelines, the fluid is grounded by installing ground plates. When there are stray potentials present in the pipeline, we recommend installing a...
Open the catalog to page 5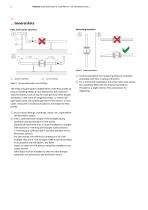
— … General data Mounting position Inlet and outlet sections Figure 5: Mounting position Vertical installation for measuring abrasive materials, preferably with flow in upward direction. B For a horizontal installation, the meter tube must always be completely filled with the measuring medium. Provide for a slight incline of the connection for degassing. A Figure 4: Inlet and outlet section, turn-off devices The measuring principle is independent of the flow profile as long as standing eddies do not extend into the measured value formation, such as may for example occur after double...
Open the catalog to page 6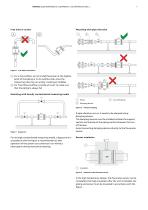
Free inlet or outlet Mounting with pipe vibration Free inflow and outflow For a free outflow, do not install flowmeter at the highest point of the piping or on its outflow side, since the measuring tube may run empty, creating air bubbles. B For free inflow/outflow, provide an invert to make sure that the piping is always full A Mounting with heavily contaminated measuring media 1 Pump 2 Damping device Figure 8: Vibration damping Figure 7: Bypass line For strongly contaminated measuring media, a bypass line in accordance with the figure is recommended so that operation of the system can...
Open the catalog to page 7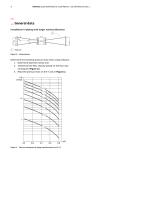
— … General data Installation in piping with larger nominal diameter 1 Reducer Figure 10: Using reducers Determine the resulting pressure loss when using reducers: 1. Determine diameter ratios d/D. 2. .Determine the flow velocity based on the flow rate nomogram (Figure 11). 3. Read the pressure loss on the Y-axis in Figure 11. Figure 11: Flow rate nomogram for flange transition piece at α/2 =
Open the catalog to page 8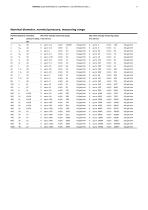
Nominal diameter, nominal pressure, measuring range Nominal diameter Standard DN Min. flow velocity measuring range Max. flow velocity measuring range
Open the catalog to page 9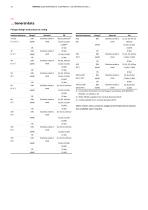
— … General data Flange design and pressure rating Nominal diameter 3 to 25 (¹⁄₁₀ to 1”) steel ASME 1) Connection dimensions for the flange in accordance with DIN2501 / EN1092−1 or ASME or JIS. 2) PN63, PN100 available from nominal diameter DN 25. steel ASME 10 bar Stainless steel or steel steel ASME 3) CL600 available from nominal diameter DN 25. Other meter sizes, pressure stages and temper
Open the catalog to page 10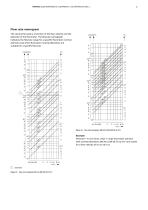
Flow rate nomogram The volume flowrate is a function of the flow velocity and the diameter of the flowmeter. The flowrate nomograph indicates the flowrate range for a specific flowmeter nominal diameter and which flowmeter nominal diameters are suitable for a specific flowrate. Figure 13: Flow rate nomogram, DN 125 to DN 1000 (5 to 40″) Example: Flowrate = 7 m3/h (max. value = range end value). Sensors with nominal diameters DN 20 to DN 65 (¾ to 2½”) are suited for a flow velocity of 0.5 to 10 m/s. 1 Example Figure 12: Flow rate nomogram DN 3 to DN 100 (10 to
Open the catalog to page 11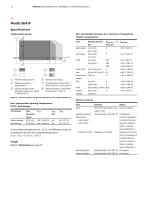
— Model SE41F Specifications Min. permissible pressure as a function of measuring medium temperature Temperature graph Hard rubber Nominal diameter Thick PTFE high 4 Stainless steel flange 2 Measuring medium temperature °C 5 Standard flange (steel): PTFE / PFA / ETFE max. 130 °C (266 °F) 3 Standard flange (steel): Hard/soft rubber max. 90/60 °C (194 to 140 °F) 6 High temperature: thick PTFE / PFA max. 180 °C (356 °F) temperature 1 Ambient temperature °C Figure 14: Measuring medium temperature dependent on the ambient temperature Sensor material Max. permissible cleaning temperature PTFE-,...
Open the catalog to page 12All ABB Measurement & Analytics catalogs and technical brochures
-
Sensyflow FMT700-P Compact
4 Pages
-
CoriolisMaster FCB100, FCH100
60 Pages
-
ProKiln GAC400
24 Pages
-
AV1 and AV2
24 Pages
-
OriMaster FPD500
24 Pages
-
AquaProbe FEA200
16 Pages
-
FTPA2000-HP260
4 Pages
-
266HSH and 266NSH
40 Pages
-
261GC, 261GG, 261GN and 261AC
44 Pages
-
LM200 Laser level transmitter
24 Pages
-
LLT100 Laser level transmitter
26 Pages
-
CoriolisMaster FCB400, FCH400
104 Pages
-
PME120-AI / PME120-AN (Contrac)
28 Pages
-
Millmate roll force systems
20 Pages
-
FTSW100 Process software
4 Pages
-
Totalflow host software
8 Pages
-
SCK
20 Pages
-
SCADAvantage™ EFM Tool
4 Pages
-
INDI-BOY DSP
8 Pages
-
CRANE-BOY / CRANE-BOYP
8 Pages
-
9QGPS5100L Tension load cell
12 Pages
-
9QGPS4500
8 Pages
-
9QGPS3100P
12 Pages
-
9QGPS2960
12 Pages
-
9QGPS2625
8 Pages
-
Ultrasonic level LST400
12 Pages
-
MB3600-HP10
5 Pages
-
MB3600-CH10
8 Pages
-
ACF5000
16 Pages
-
Diode laser analyser LS4000
4 Pages
-
Magnos28
10 Pages
-
Dynamic QR Code
4 Pages
-
EL3060
8 Pages
-
Pressductor Radial load cells
20 Pages
-
HP30
4 Pages
-
Aztec ATS430
12 Pages
-
LMS200
12 Pages
-
PGC5000
8 Pages
-
LGR-ICOS 927S
4 Pages
-
Recording and Control
20 Pages
-
2600T Pressure Transmitters
12 Pages
-
TZIDC and TZIDC-200
8 Pages
-
ProcessMaster FEP610
8 Pages
-
ALSCAN Brochure
6 Pages
-
MR Series
2 Pages
-
Emission Monitoring
8 Pages
-
Turbidity Systems 4670 Series
16 Pages
-
Sodium Monitor Model 8036
8 Pages
-
Aztec 600 Iron Analyzer
12 Pages
-
First for Liquid Analysis
16 Pages
-
ABB product catalog
32 Pages
-
process photometer
6 Pages
-
Sodium Monitor Model 8036
8 Pages