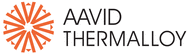
Catalog excerpts
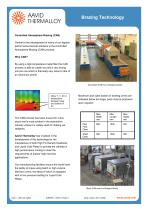
Brazing Technology Controlled Atmosphere Brazing (CAB) Central to the development of many of our highest performance thermal solutions is the Controlled Atmosphere Brazing (CAB) process. Why CAB? By using a high temperature metal filler the CAB process is able to create not only a very strong join but one which is thermally very close to that of an Aluminum profile Automated CAB line in Bologna facility Delta T = 1.2C in temperature between base and bottom of fin. The CAB process has been around for many years and is most evident in the automotive industry where it is widely used for making car radiators. Aavid Thermalloy has invested in the development of this technology for the manufacture of both High Fin Density Heatsinks and Liquid Cold Plates to provide the ultimate in high performance cooling to meet the requirements of todays’ high heat flux applications. Maximum part sizes based on existing ovens are indicated below but larger parts may be produced upon request; Fast Flow Oven Static Oven Our manufacturing facilities around the world have the ability to braze using batch or high volume fast flow ovens, the latest of which is equipped with in line pressure testing for Liquid Cold Plates. Static CAB ovens in Bologna facility
Open the catalog to page 1
Brazing Process Degreasing Cleaning Adding flux and filler Components preparation Component Assembly + Jigging Leakage test Mechanical strength test All components to be brazed are first cleaned and pre assembled using jigs A paste combining a filler and flux is added to any surfaces to be joined. The flux remains inert until brazing temperature is reached at which point it acts eliminating any oxide layer present At a slightly higher temperature the filler melts and flows filling any gaps. Brazed surface suitable for chromate / painting / anodizing Flux is non-corrosive* No need for flux...
Open the catalog to page 2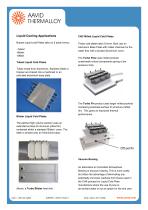
Liquid Cooling Applications CNC Milled Liquid Cold Plates Brazed Liquid cold Plates take on 3 basic forms; These cold plates take 2 forms. Both use an Aluminum Base Plate with milled channels for the water flow with a brazed Aluminium cover. -Tubed -Blister -Milled Tubed Liquid Cold Plates Tubes made from Aluminium, Stainless Steel or Copper are brazed into a machined or an extruded aluminium base plate. Blister Liquid Cold Plates The Turbo Flow uses milled pockets underneath critical components giving a low pressure drop. The Turbo Fin product uses larger milled pockets containing extended...
Open the catalog to page 3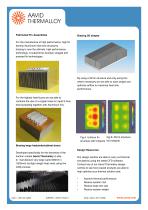
For the manufacture of high performance, high fin density Aluminium heat sink structures brazing is now the ultimate high performance technology. It outperforms bonded, swaged and pressed fin technologies. By using a 3D fin structure and only using fins where necessary we are able to save weight and optimise airflow to maximise heat sink performance. For the highest heat fluxes we are able to combine the use of a copper base for rapid X-Axis heat spreading together with Aluminium fins. Fig B. 3D fin structure. Fig A. Uniform fin structure with hotspots No hotspots Brazing large...
Open the catalog to page 4All Aavid Thermalloy catalogs and technical brochures
-
HydroSink™
4 Pages
-
Spotlight LED Heatsink 60W
2 Pages
-
LED Heatsink R87-60
3 Pages
-
LED Heatsink L100-180
2 Pages
-
LED Heatsink L100-270
3 Pages
-
LED Heatsink R150-170
2 Pages
-
Vicor Bricks
4 Pages
-
Half Brick
2 Pages
-
Quarter Brick
2 Pages
-
Eighth Brick
2 Pages
-
SOFTFLEX GAP FILLER
1 Pages
-
Embedded Solutions
2 Pages
-
Standard Products Catalog
116 Pages
-
RazorJet™ Series
2 Pages
-
Dual Cool Jet
1 Pages
-
Heat Pipes
6 Pages
-
Liquid Cooled Solutions
2 Pages
-
HydroSink?
4 Pages