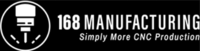
Catalog excerpts
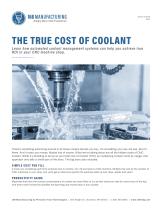
Simply More CNC Production THE TRUE COST OF COOLANT Learn how automated coolant management systems can help you achieve true ROI in your CNC machine shop. There’s something swimming around in all those coolant barrels you buy. It’s something you may not see. But it’s there. And it costs you money. Maybe lots of money. What we’re talking about are all the hidden costs of CNC coolant. While it’s tempting to arrive at your total cost of coolant (TCC) by multiplying coolant costs by usage, that approach only tells a small part of the story. The big story also includes: It costs you something each time someone has to monitor, mix, fill and report a CNC machine. Multiply this cost by the number of CNC machines in your shop, and you’ll get an idea how quickly this expense adds up over days, weeks and years. Machines that have the correct concentrations of coolant are more likely to run at their maximum rate for more hours of the day. And every extra minute the spindles are spinning puts money back in your pocket. 168 Manufacturing by Precision Tool Technologies | 924 Wright St., Brainerd, MN 56401 | 1.800.450.8665 | www.1
Open the catalog to page 1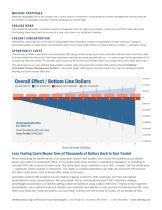
Machine stoppages due to low coolant are a costly source of downtime. Automating the coolant management process reduces the number of stoppages for each machine, keeping your uptime high. One benefit of automatic, consistent coolant management with the right concentration is that your tools don’t wear as quickly. Purchasing fewer tools over the course of a year cuts down on a significant expense. Oftentimes, machinists err on the side of using higher-than-necessary coolant concentrations in their machines. Using an automated system to keep these concentrations within the correct range means...
Open the catalog to page 2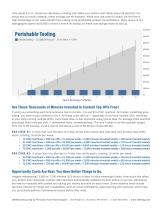
How would a 5- to 10-percent decrease in tooling cost affect your bottom line? What about 25 percent? For shops that cut exotic material, these savings can be dramatic. While your use case is unique, we find that a high percentage of our users benefit from having more predictable coolant concentrations. Many shops in our demographic spend $100,000 or more a month on tooling, so these cost savings really do add up. $1,000,000 Perishable Tooling TOOLING SAVINGS Years Running FullShop™ Are Those Thousands of Minutes Invested in Coolant Top-Offs Free? It costs you something each time someone...
Open the catalog to page 3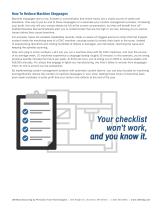
How To Reduce Machine Stoppages Machine stoppages due to low, flooded or concentration that wreck havoc are a costly source of waste and downtime. One way to put an end to these stoppages is to automate your coolant management process, increasing your profit. Not only will your sumps always be full at the correct concentration, but they will benefit from IoTenabled features that automatically alert you to coolant levels that are too high or too low, allowing you to resolve issues before they cause downtime. For example, these IoT-enabled capabilities recently made us aware of clogged...
Open the catalog to page 4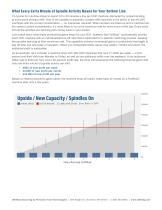
What Every Extra Minute of Spindle Activity Means for Your Bottom Line It’s typical for machine shops to spend 10 to 20 minutes a day per CNC machine, distracted by coolant-tending at some point during a shift. One of the upsides to automatic coolant refill machines is the ability to top-off CNC machines with the correct concentration — no manpower required. When workers are freed up and a machine has the correct coolant concentration, it’s more likely to run at its maximum rate for more hours of the day. Every extra minute the spindles are spinning puts money back in your pocket. Let’s...
Open the catalog to page 5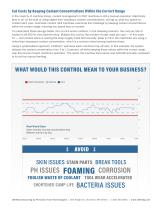
Cut Costs by Keeping Coolant Concentrations Within the Correct Range In the majority of machine shops, coolant management in CNC machines is still a manual operation. Machinists tend to err on the side of using higher-than-necessary coolant concentrations, driving up what you spend on coolant each year. Automatic coolant refill machines overcome this challenge by keeping coolant concentrations within the correct range, meaning you spend less on coolant. To understand these savings better, let’s crunch some numbers. In the following scenario, the cost per tote of coolant is $9,500 for one...
Open the catalog to page 6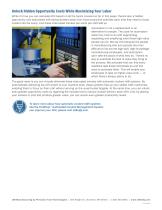
Unlock Hidden Opportunity Costs While Maximizing Your Labor While it’s true you can calculate ROI based on all the topics covered so far in this paper, there’s also a hidden opportunity cost associated with taking workers away from more productive activities each time they need to dump coolant into the sump. And these interrupted minutes per sump per shift add up. Automation is not a replacement or an alternative for people. The case for automation really has more to do with augmenting, expanding and amplifying what those high-value people can do. We say this because the people in...
Open the catalog to page 7