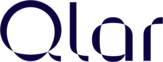

カタログの抜粋
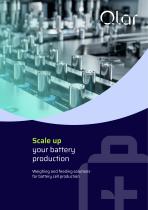
Scale up your battery production Weighing and feeding solutions for battery cell production
カタログの1ページ目を開く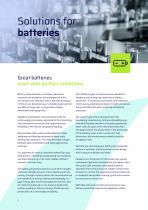
Great batteries start with perfect conditions Battery cell production is complex. Maximum precision and protection for employees and the environment are required. This is because producers of lithium-ion batteries have to handle materials that are difficult to process, in some cases highly flammable and highly toxic. Two different types of processes are possible for weighing and mixing raw materials in battery production. In continuous processes, the material is continuously weighed and dosed; in batch processes, there are breaks between weighing and dosing processes. Weighers and feeders...
カタログの2ページ目を開く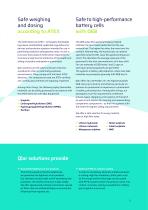
Safe weighing and dosing according to ATEX Safe to high-performance battery cells with OEB The ATEX Directive (ATEX = Atmospère Explosible) lays down standardized, applicable regulations for devices and protective systems intended for use in potentially explosive atmospheres areas. Its aim is to ensure that products fulfil certain requirements, to ensure a high level of protection of the health and safety of persons and goods is guaranteed. The OEB value (Occupational Exposure Band) indicates the toxic hazard potential that the raw material has. The higher the value, the more toxic the...
カタログの3ページ目を開く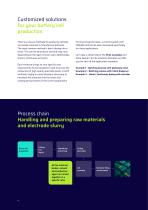
Customized solutions for your battery cell production There are various methods for producing cathode and anode mixtures to manufacture batteries. The most common method is batch dosing into a mixer. This can be done dry or wet and may vary depending on the type of mixer used. Additionally, there is continuous extrusion. Each variation brings its own specifics and requirements to the equipment used to ensure the production of high-quality electrode paste. In both methods, highly accurate dosing is necessary to introduce the materials into the mixer and subsequent processes in the correct...
カタログの4ページ目を開く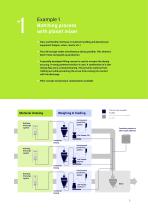
Example 1 Batching process with planet mixer C lear and flexible interfaces to material handling and downstream equipment (hopper, mixer, reactor etc.) T he LIW concept makes simultaneous dosing possible. This shortens batch times and speeds up production. A specially developed filling concept is used to increase the dosing accuracy. A newly patented solution is used. A combination of a fast closing flap and a screwend bearing. This prevents material from trickling out while preventing the screw from coming into contact with the discharge. F ilter concept and pressure compensation available...
カタログの5ページ目を開く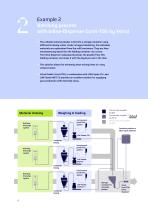
Example 2 Batching process with Inline-Disperser Conti-TDS by Ystral he cathode material powder is fed into a storage container using T differential dosing scales. Under nitrogen blanketing, the individual materials are replenished from the refill containers. They are then simultaneously dosed into the holding container via a screw. The Inline Disperser subsequently draws the powder from this holding container and mixes it with the liquid pre-set in the tank. his solution allows for extremely short mixing times in a very T compact space. stral GmbH’s Conti-TDS, in combination with LIW...
カタログの6ページ目を開く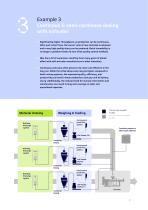
Example 3 Continous & semi-continous dosing with extruder ignificantly higher throughputs, as production can be continuous. S After just a short time, the correct ratio of raw materials is achieved and a very high quality slurry can be produced. Batch traceability is no longer a problem thanks to new inline quality control methods. lar has a lot of experience resulting from many years of joined Q effort with with extruder manufacturers in other industries. ontinuous extrusion often proves to be more cost-effective in the C long run. While the initial setup costs may be higher compared to...
カタログの7ページ目を開く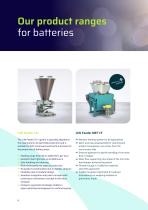
Our product ranges for batteries LIW Feeder CS+ The LIW Feeder CS+ system is specially adapted to the requirements of electrode production and is suitable for both continuous and batch processes for the production of battery mass. Feeding range from 30 to 3,000 liters per hour Excellent dust tightness up to OEB level 4 Safe handling and cleaning Risk minimization for users in production No product contamination due to metallic abrasion Flexibility due to modular design Seamless integration into plant concepts with continuous containment concept to limit dust emission Compact, asymmetrical...
カタログの8ページ目を開く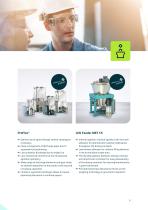
ProFlex® Optimal use of space through vertical, rectangular containers Close arrangement of discharge pipes due to asymmetrical positioning Low-pulsation discharge due to angled cut Low mechanical interference due to balanced agitation geometry Wide range of discharge elements and gear ratios for optimal adaptation to the product and required conveying capacities Compact, asymmetrical design allows for spaceoptimized placement in confined spaces LIW Feeder MET CS Internal agitation (vertical agitator) with low wall adhesion for optimal bulk material mobilization throughout the dosing...
カタログの9ページ目を開く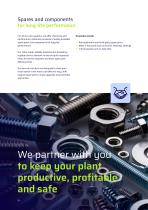
Spares and components for long-life performance For all our core systems, we offer chemicals and performance materials processors readily available spare parts and components for long-life performance. Our tailor-made, reliable solutions are backed by a global service network to ensure quick response times for service requests and short spare part delivery times. Examples include Refurbishment and third-party spare parts Wear & tear parts such as screws, bearings, sealings Critical spares such as load cells Our service contracts are designed to meet your exact needs in the most...
カタログの10ページ目を開く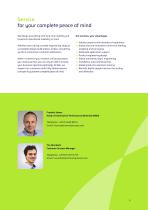
Service for your complete peace of mind We design everything with long-term stability and maximum operational reliability in mind. Whether we’re doing a simple engineering study or a complete design-build project, at Qlar, everything we do is centered on customer satisfaction. When it comes to your mission-critical processes, you need a partner you can rely on 100 % to keep your business operating optimally. At Qlar, we support our customers with fully tailored service concepts to guarantee complete peace of mind. Our services, your advantages Industry experts with decades of experience...
カタログの11ページ目を開くSchenck Process Holding GmbHのすべてのカタログと技術パンフレット
-
FulFiller ®
8 ページ
-
CONiQ® Cloud
1 ページ
-
MULTIRAIL® BogieLoad pro
20 ページ
-
Pharmaceutical industry
10 ページ
-
MULTIRAIL®
16 ページ
-
Company overview
20 ページ
-
We make processes work
20 ページ
-
LinaClass® screens
6 ページ
-
CONiQ®
12 ページ
-
MCPP
12 ページ
-
ModuPlasma
8 ページ
-
MaxiStore®
8 ページ
-
SacMaster®
8 ページ
-
Food industry
20 ページ
-
Training that delivers!
38 ページ
-
Cement industry
16 ページ
-
TEDO Conveyors
18 ページ
-
Drop forged chain
8 ページ
-
RoCon® Series 6
8 ページ
-
SPro screen panels
12 ページ
-
Power industries
16 ページ
-
Tidal Series 5
6 ページ
-
Screen rebuilding
4 ページ
-
RotoScrew
2 ページ
-
DWB
4 ページ
-
MultiFlex
4 ページ
-
LinaClass®
6 ページ
-
Stock Valves
8 ページ
-
Product Overview
8 ページ
-
SacMaster
1 ページ
-
MULTIBELT®
1 ページ
-
MULTIDOS® VDP
1 ページ
-
DISOCONT ®
4 ページ
-
INTECONT® PLUS
4 ページ
カタログアーカイブ
-
We make processes work
16 ページ
-
MULTIRAIL® WheelLoad
2 ページ
-
MULTIRAIL® WheelScan
2 ページ
-
MULTIRAIL® LegalWeight
2 ページ
-
MULTIDOS® L
4 ページ
-
MULTIGRAV®
4 ページ
-
ProFlex® C
2 ページ
-
Mobile Touch Panel FSB
2 ページ
-
DISOMAT® Satus
4 ページ
-
INTECONT® Opus
4 ページ
-
weighing sensor
1 ページ
-
Force exciters
4 ページ
-
MULTISTREAM® B
4 ページ
-
MULTICOR® R 450
4 ページ
-
MULTIDOS® E
4 ページ
-
MULTIDOS® M
4 ページ