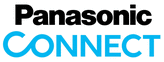
グループ: Panasonic Factory Solutions Europe

カタログの抜粋
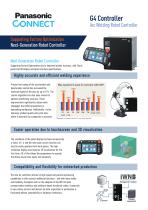
Arc Welding Robot Controller Supporting Factory Optimization Next-Generation Robot Controller Next Generation Robot Controller Supporting Factory Optimization due to Improved motion accuracy, with Touch panel and 3D display and Open interface specifications. Highly accurate and efficient welding experience Precise fine-tuning of the acceleration and deceleration control has increased the maximum speed of the axes by up to 27%. The control algorithm has also been revised to optimize positioning accuracy. These improvements significantly reduce work stoppages that affect productivity in demanding workplaces. Additionally, it also improves product quality and cycle time, which is essential for companies to succeed. Max speed of 6 axes (in contrast with G3)* 127% 120% Average Average of main of all *Example of measurement in our environment Easier operation due to touchscreen and 3D visualization The resolution of the panel display has been increased by a factor of 1.6 and the new touch screen function can also be easily operated with work gloves. The highresolution display also features 3D visualization for the first time. All of this allows the programmer to operate the device much more easily and intuitively. Compatibility and flexibility for networked production The new G4 controller utilizes its high-speed and parallel processing capabilities to offer several additional functions - and with more safety and flexibility. Examples such as the adoption of the OPC UA open communication interface and software-based functional safety. Connection to new safety sensors and devices for data acquisition or automation is facilitated without compatibility or hardware limitations.
カタログの1ページ目を開く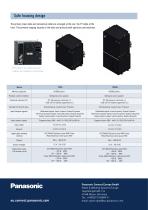
Safe housing design The primary input cable and connection cable are arranged at the rear, the TP cable at the front. This prevents tripping hazards at the sides and protects both operators and machines. M-C/built-in external axis cables arranged on the back. Memory capacity Position control method Software servo system Software servo system TP: SD memory card slot x 1 USB 2.0 (Hi-Speed supported) x 2 TP: SD memory card slot x 1 USB 2.0 (Hi-Speed supported) x 2 Simultaneous 6 axes (max. 27 axes) Simultaneous 6 axes (max. 27 axes) Number of control axes Input/output signals Dedicated signal:...
カタログの2ページ目を開くPanasonic Robot & Welding system solutionsのすべてのカタログと技術パンフレット
-
PC-Software DTPS
10 ページ
-
Wire Booster
2 ページ
カタログアーカイブ
-
PAN1326C2
1 ページ
-
Power Choke Coil
19 ページ
-
POSCAP
40 ページ
-
E-Bike Systems
12 ページ
-
PAN1760A
2 ページ
-
PAN1740
41 ページ
-
PAN1761
2 ページ
-
EUROPEAN E-CALL
2 ページ
-
EMERGENCY LIGHTING
2 ページ
-
PAN1326C2 2019
48 ページ
-
PAN1762
17 ページ
-
PAN1326C
40 ページ
-
PAN9026
82 ページ
-
PAN1326 Design Guide
22 ページ
-
Panasonic Torches
2 ページ
-
Microcomputer
24 ページ
-
Handling Robots
2 ページ
-
TAIWERS-Welding Solution
12 ページ
-
Panasonic Positioner
4 ページ
-
DTPS G3-Software
4 ページ
-
G3 Robot Controller
1 ページ
-
YD-350GB2
2 ページ
-
DTPS-G3
4 ページ
-
WG3 Welding Robots
12 ページ
-
SP-MAG Process
2 ページ
-
TIG Filler System
1 ページ
-
PerformArc C Series
1 ページ
-
PerformArc TT Series
1 ページ
-
PerformArc MT Series
1 ページ
-
PerformArc ET Series
1 ページ
-
TAWERS WG3 Series
12 ページ
-
Positioners
4 ページ
-
Panasonic Eco ideas
2 ページ