
Catalog excerpts
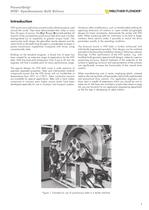
HTD synchronous belt drives are technically refined products usedaround the world. They have demonstrated their utility in more than 20 years of service. The H igh T orque D rive belt exhibits alltransmit of the conventional synchronous belt drive and is further distinguished by its capability to greater torque loads. The semicircular tooth shape, the glass-fiber tensile element and the nylon finish on the teeth have brought a considerable increase in power transmission capabilities compared with drives using conventionally belts.Building on the standard program, a broad line of types...
Open the catalog to page 3
The high power transmission capacities of HTD belt, along withtheir compact dimensions and low weights, offer clear advantages compared with other drive concepts. The high degree of economy for the HTD synchronous belt drivesis the product of the properties mentioned above including ideal power transmission, a variety of types, compact design, minimum energy requirements, environmental acceptability, freedom from maintenance requirements, etc. In addition, the High performance in limited space and at low weight Economy > Positive engagement of the HTD teeth with the grooves of thedrive...
Open the catalog to page 4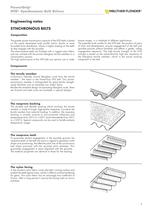
The greater power transmission capacity of the HTD belts is basedon the newly developed tooth profile which, thanks to more favorable force distribution, allows a higher loading on the teeth as they engage with the sprocket. The wear-resistant teeth are finished with a rugged nylon fabric and are unitized with the proven fiberglass tensile members in a vulcanization process. The high performance of the HTD belt now permits use in widertorque ranges, in a multitude of different applications.The patented tooth profile for the HTD belt, the product of years of trials and development, ensures...
Open the catalog to page 5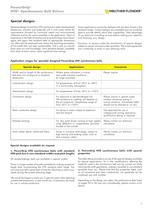
Standard-design PowerGrip HTD synchronous belts (standardizeddimensions, structure and materials) will in most cases satisfy the requirements dictated by functional needs and environmental influences and by the space available in the application. Years of experience in the field of mechanical drive technology have shown again and again that standard belts of appropriate dimensions can often also be employed even where the operating parameters at first made their use seem questionable. That is why you should draw upon our vast knowledge, since standard designs, available from stock at short...
Open the catalog to page 7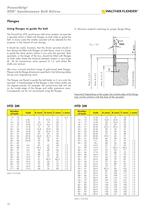
D: Minimum material overhang for proper flange fitting The PowerGrip HTD synchronous belt drive systems incorporatea sprocket which is fitted with flanges on both sides to guide the belt. In many cases the smaller sprocket will be selected for this purpose, in the interest of cost savings.It should be noted, however, that the driven sprocket should infact always be fitted with flanges on both faces, since it is easier to guide the slack section where it runs onto the sprocket. Both sprockets, or the larger of the two, should be fitted with flanges on both sides where the distance between...
Open the catalog to page 12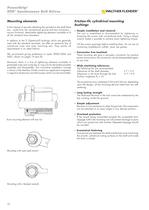
In the interest of securely attaching the sprocket to the shaft thereare aside from the conventional groove and key connectors ֖ various frictional, detachable tightening elements available to fit all the standard bore diameters.In addition to the TL (TaperLock Simple installation and removal The unit is assembled or disassembled by tightening or loosening the screws with conventional tools. Using a torque wrench makes it possible to achieve exact tightening torque.Oil the screws sparingly before installing them. Do not use oilcontaining molybdenum sulfide; never use grease. > ֮ ) bushings...
Open the catalog to page 16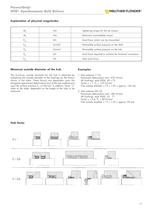
M > S NmTightening torque for the set screws M > t NmMaximum transmittable torque P > ax kNAxial force which can be transmitted P > 2 W N/mm Permissible surface pressure on the shaft P > 2 N N/mm Permissible surface pressure on the hub P > O kNAxial force required to achieve the frictional connectionP > tot kNTotal axial force > The minimum outside diameter for the hub is obtained by multiplying the outside diameter of the bushings by the factors shown in the table. These factors are dependent upon the elongation (permanent deformation) limit of the hub material and upon the surface...
Open the catalog to page 17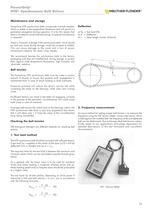
PowerGrip HTD synchronous belts incorporate a tensile memberwhich is stable in the longitudinal dimension and will permit no permanent elongation during operation. It is for this reason that there is no need to correct belt tensioning; no special maintenance is required.There is, however, a danger if the synchronous belts, which shouldbe laid very loose during storage, could be crimped or folded. This can cause damage to the cords and a loss of power transmission capacity. Do never crimp sharply.We recommend leaving the synchronous belts in the factorypackaging until they are installed and,...
Open the catalog to page 23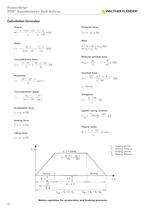
Torque Frictional force > 3 d M =P 9.55 10 =F > U w 3 [Nm]n2 10 F > R = m g [N] Mass Power շ v[kW]9.55 10 m = m > L + m > R + m > Zred [kg]mit m P =M n=F > U 3 = I m 10 > 3 R W G Reduced sprocket mass Circumferential force > Z B2 3 3 m > Zred =m ( 1 + d )[kg]2d F > U =P 10 =M 2 10 [N]vd > a2 w Sprocket mass Revolution > a2 ז d > B2 ) 7 B > 3 m > Z =(d > 6 [kg]4 · 10 n =19.1 10 v[min > -1 ]d > w ς = Density Circumferential speed nm19.1 10 Elongation v =d > w 3 sec ∆ I 100[%]I = > t Acceleration force Specific spring constant F > a = m a [N] 100[N] C > admissible spec =F...
Open the catalog to page 26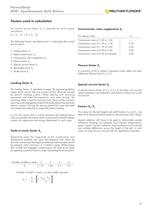
An overall service factor S > G is required for drive systemcalculations:S > 3 G = S > 2 (S > 1 + S > 3 + S > 4 - S > 5 )The following factors are determinant in calculating the overallservice factor:1. Loading factor S For step-up ratiosS > 3 Transmission ratio of 1.00 to 1.24זTransmission ratio of 1.25 to 1.740.10Transmission ratio of 1.75 to 2.490.20Transmission ratio of 2.50 to 3.490.30Transmission ratio of 3.50 and greater0.40 > 1 2. Teeth-in-mesh factor S > 2 3. Transmission ratio supplement S > 3 4. Flexure factor S > 4 5. Special service factor S > 5 4 6. Belt length factor S > 6 7....
Open the catalog to page 27All Walther Flender catalogs and technical brochures
-
timing belts neoprenes
108 Pages
-
WF_TM_Nano
1 Pages
-
ML Clamping Sets
30 Pages
-
PolyChain_timingbelts
48 Pages
-
frequency inverter Serie M/N
24 Pages
-
Flatbelts WF Lift Power
12 Pages