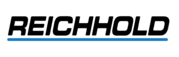
Catalog excerpts
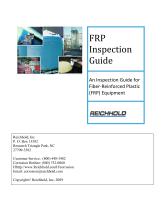
FRP Inspection Guide An Inspection Guide for Fiber‐Reinforced Plastic (FRP) Equipment Reichhold, Inc P. O. Box 13582 Research Triangle Park, NC 27709-3582 Customer Service: (800) 448-3482 Corrosion Hotline: (800) 752-0060 Hhttp://www.Reichhold.comH/corrosion Email: corrosion@reichhold.com Copyright© Reichhold, Inc, 2009
Open the catalog to page 1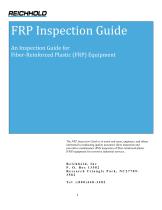
FRP Inspection Guide An Inspection Guide for Fiber‐Reinforced Plastic (FRP) Equipment The FRP Inspection Guide is to assist end users, engineers, and others interested in conducting quality assurance (QA) inspection and preventive maintenance (PM) inspection of fiber-reinforced plastic (FRP) equipment for corrosive industrial services.. . Reichhold, Inc P. O. Box 13582 Research Triangle Park, NC277093582 Tel :(800)448-3482
Open the catalog to page 2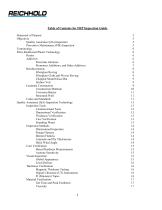
Quality Assurance (QA) Inspection 5 Preventive Maintenance (PM) Inspection 5 Fiber-Reinforced Plastic Technology 6 Promoters, Inhibitors, and Other Additives 7 Fiberglass Cloth and Woven Roving 9 Chopped Strand Glass Mat 9 Quality Assurance (QA) Inspection Technology 13 Common Hand Tools 13 Helix Wind Angle 14 Barcol Hardness Measurements 15 Magnetic Thickness Testing 16 Digital Ultrasonic (UT) Instruments 16 Gel Time and Peak Exotherm 17
Open the catalog to page 3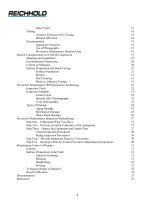
Acoustic Emission (AE) Testing 18 Preventive Maintenance Baseline Data 19 Special Considerations for Field QA Inspection 19 Surface Preparation and Bond Testing 21 Bond or Adhesion Testing 21 Preventive Maintenance (PM) Inspection Technology 23 Preventive Maintenance Inspection Methodology 27 Step One - Understand What You Have 27 Step Two - Perform an Initial Evaluation of the Equipment 27 Step Three - Inspect the Equipment and Gather Data 27 Vessel Inspection Procedures 28 Piping Inspection Procedures 30 Step Four - Perform Immediate Repairs, if Necessary 30 Step Five - Develop a Plan for...
Open the catalog to page 4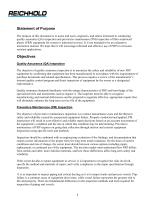
Statement of Purpose The purpose of this document is to assist end users, engineers, and others interested in conducting quality assurance (QA) inspection and preventive maintenance (PM) inspection of fiber-reinforced plastic (FRP) equipment for corrosive industrial services. It is not intended to be an exhaustive instruction manual. We hope that it will encourage informed and effective use of FRP in corrosionresistant applications. Objectives Quality Assurance (QA) Inspection The objective of quality assurance inspection is to maximize the safety and reliability of new FRP equipment by...
Open the catalog to page 5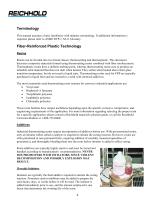
Terminology This manual assumes a basic familiarity with industry terminology. If additional information is required, please refer to ASME RTP-1, M-11 Glossary. Fiber-Reinforced Plastic Technology Resins Resins can be divided into two broad classes: thermosetting and thermoplastic. This document discusses composite materials formed using thermosetting resins combined with fiber reinforcement. Thermoplastic resins have a definite melting point, whereas thermosetting resins cure to produce an infusible solid material that does not melt when heated. They soften when heated above their glass...
Open the catalog to page 6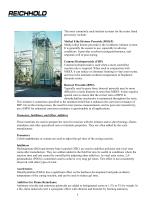
The most commonly used initiator systems for the resins listed previously include: Methyl Ethyl Ketone Peroxide (MEKP) Methyl ethyl ketone peroxide is the workhorse initiator system. It is generally the easiest to use, especially in adverse conditions. It provides excellent curing performance, and responds well to post-curing. Cumene Hydroperoxide (CHP) Cumene hydroperoxide is used when a more controlled reaction rate is required. When used in conjunction with MEKP, it can reduce or eliminate foaming in vinyl ester resins, and lower the laminate exotherm temperature of bisphenol fumarate...
Open the catalog to page 7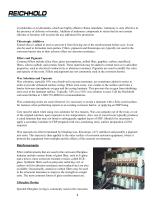
oxychlorides or oxybromides, which are highly effective flame retardants. Antimony is only effective in the presence of chlorine or bromine. Addition of antimony compounds to resins that do not contain chlorine or bromine will not provide any additional fire protection. Thixotropic Additives Fumed silica is added to resin to prevent it from flowing out of the reinforcement before cure. It can also be used to formulate resin putties. Fillers, pigments and thixotropes are typically not used in the corrosion barrier due to their adverse effect on corrosion resistance. Fillers and Pigments...
Open the catalog to page 8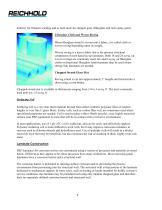
industry for filament winding and as feed stock for chopper guns (fiberglass and resin spray guns). Fiberglass Cloth and Woven Roving When fiberglass strand is woven into a fabric, it is called cloth or woven roving depending upon its weight. Woven roving is a heavy fabric that is the primary structural component of most hand lay-up laminates. Both 18 and 24 oz/sq. yd woven rovings are commonly used. Six and 8 oz/sq. yd fiberglass cloths or directional fiberglass reinforcements may be used where strong, thin laminates are needed. Chopped Strand Glass Mat Roving strand is cut into...
Open the catalog to page 9
Construction Methods FRP materials are products of both the raw materials and the construction process used. The most commonly used processes for producing corrosion-grade FRP parts are filament winding, contact molding, centrifugal molding, matched die compression molding, and pultrusion. Filament-wound parts are relatively inexpensive to make and are characterized by a high strength-toweight ratio. Strength and stiffness are gained by winding tapes, random chopped glass, or glass roving in a spiral pattern, commonly referred to by its helix angle (the angle between the longitudinal axis...
Open the catalog to page 10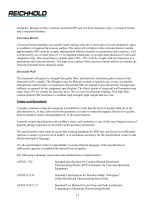
resistance. Because of this, corrosion-resistant FRP uses two basic laminate types: a corrosion barrier and a structural laminate. Corrosion Barrier Corrosion barrier laminates are usually made starting with one or more plies of resin saturated C-glass or synthetic veil against the process surface. The resin-rich veil plies in the corrosion barrier contain approximately 90% resin by weight, making them effective barriers to permeation and corrosion. Veil is followed by two or more plies of 1.5 oz chopped strand mat, or an equivalent thickness of resin and chopped roving. This second layer...
Open the catalog to page 11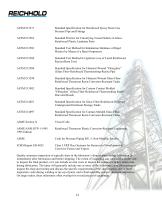
Standard Specification for Reinforced Epoxy Resin Gas Pressure Pipe and Fittings Standard Practice for Classifying Visual Defects in GlassReinforced Plastic Laminate Parts Standard Test Method for Indentation Hardness of Rigid Plastics by Means of a Barcol Impressor Standard Test Method for Ignition Loss of Cured Reinforced Resins (Burn Test) Standard Specification for Filament-Wound “Fiberglass” (Glass Fiber-Reinforced Thermosetting-Resin) Pipe Standard Specification for Filament-Wound Glass-FiberReinforced Thermoset Resin Corrosion-Resistant Tanks Standard Specification for Custom Contact...
Open the catalog to page 12All Reichhold catalogs and technical brochures
-
UROTUF® F275-M-75
2 Pages
-
EPOTUF® 38-698
2 Pages
-
F600-W-40
2 Pages
-
UROTUF®
7 Pages
-
DION® IMPACT 9133
2 Pages
-
UROTUF® Water-borne Urethane
4 Pages
-
BioiPreferred® Guideline
2 Pages
-
NORPOL® ULTIMATE GELCOAT
2 Pages
-
NORPOL® SVX Gelcoat
2 Pages
-
NORPOL® SVG Gelcoats
3 Pages
-
NEW NORPOL® SRG GELCOAT
2 Pages
-
DION® Corrosion Guide
45 Pages
-
POLYLITE ® 3354225
3 Pages
-
EPOTUF® 38-698
2 Pages
-
Improved vinyl ester technology
21 Pages
-
UROTUF® F600-W-40
2 Pages
-
UROTUF® E300-W-40
2 Pages
-
Corrosion Guide
45 Pages
-
Coating Resins Catalog
35 Pages
-
BECKOSOL AQ®
12 Pages
-
AROFLINT® Flyer
2 Pages
-
Material Selection Guide
77 Pages
-
Vacuum Foil Infusion
19 Pages
-
RTM Light
15 Pages
-
Pultrusion (Europe)
3 Pages
-
A Reichhold Company Overview
11 Pages
-
NORPOL® VBC Barriercoat
3 Pages
-
NORPOL® GI
3 Pages
-
NORPOL® CPG
4 Pages
-
Pultrusion (EMEA)
3 Pages
-
NORPOL® SVG Gelcoats
4 Pages
-
Fire Retardant (EMEA)
15 Pages
-
Bonding Paste (EMEA)
15 Pages
Archived catalogs
-
Vacuum Foil/ RTM Process (EMEA)
11 Pages
-
Tooling System (EMEA)
11 Pages
-
SMC/ BMC (EMEA)
3 Pages