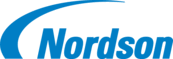

Catalog excerpts
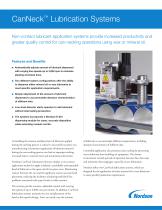
CanNeck™ Lubrication Systems Non-contact lubricant application systems provide increased productivity and greater quality control for can-necking operations using wax or mineral oil. Features and Benefits Automatically adjusts amount of lubricant dispensed with varying line speeds up to 3,000 cpm to minimize pleating and black lines. Two different system configurations offer the ability to dispense either mineral oil or wax lubricants to meet specific application requirements. Simple adjustment of the amount of lubricant dispensed to accommodate abrasion characteristics of different inks. L ow-level detector alerts operator to add lubricant without interrupting production. The systems incorporate a Nordson E-201 dispensing module for clean, accurate deposition while extending module coil life. Controlling the amount and placement of lubricant applied during the necking process is critical to successful two-piece can manufacturing. Inconsistent application of lubricant material during the can-necking process can lead to improper necking, increased rejects, material waste and maintenance downtime. Nordson CanNeck Lubrication Systems employ a non-contact application method to apply a defined, controllable and repeatable bead of lubricant to the open end of two-piece cans. Eliminating contact between the can and the applicator assures accurate bead placement, reducing the incidence of pleating and black line problems associated with typical wick or roller systems. The systems provide accurate, adjustable control with varying line speeds of up to 3,000 cans per minute. In addition, CanNeck lubrication systems maintain the size and placement of the bead as line speeds change. Users can easily vary the amount of lubricant to accommodate different requirements, including abrasion characteristics of different inks. Controlled application also promotes clean tooling by preventing excess lubricant from building on equipment. The cleaner environment extends periods of operation between line clean-ups and minimizes line stoppages caused by excess lubrication. Nordson offers two CanNeck lubrication systems, which are designed for the application of either mineral oil or wax lubricants to meet specific production requirements.
Open the catalog to page 1
CanNeck™ Lubrication Systems The CanNeck System for Wax Lubricants CanNeck Lubrication System Controller The CanNeck wax lubrication system is designed for the controlled application of wax lubricants. The system consists of a low-level detector, pattern control timer, heated hose, heated electric gun, low-pressure pneumatic piston pump, and a Nordson Model 3500 Applicator equipped with MultiScan® controls for exceptional temperature control stability. Both CanNeck lubrication systems use a similar package to control gun operation. The Model 3500 Applicator has a 6:1 ratio, dual-acting,...
Open the catalog to page 2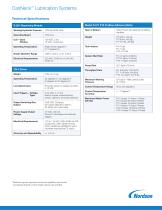
CanNeck™ Lubrication Systems Technical Specifications Model P4 P7 P10 ProBlue Adhesive Melter Operating Speed Rated at 350 degrees F (177 degrees C) Nozzle Diameter Range Electrical Requirements Tank Volume System Melt Rate Operating Temperature Piston Pump with external circulating manifold Throughput Rate Pump Rate Working Hydraulic Pressure Operating Temperature 32 degrees to 140 degrees F (0 degrees to 60 degrees C) Maximum Working Pressure 575 psi 6:1 Ratio piston pump (3.7 mPa) Line Speed Input Proximity sensor to analog converter, 0-10 VDC Control Temperature Range Input Triggers –...
Open the catalog to page 3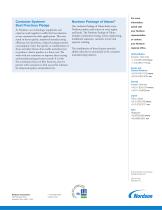
Container Systems’ Best Practices Pledge At Nordson, our technology, equipment and expertise work together to offer the best solutions to our customers for their applications. This may result in better quality, improved manufacturing efficiency, less downtime, reduced coating material consumption, faster line speeds, or combinations of these and other factors that enable manufacturers to produce a better product at a lower cost. We work with our customers to improve their coating and manufacturing processes overall. It is with this continuous focus on Best Practices, that we partner with...
Open the catalog to page 4All Nordson Industrial Coating Systems catalogs and technical brochures
-
Excel 2000
4 Pages
-
ColorMax 2
8 Pages
-
Bulk Powder Feed System
2 Pages
-
ColorMax 3
5 Pages
-
DR Pump
2 Pages
-
Disposable Mixers
4 Pages
-
Wafer Testing Solutions
4 Pages
-
4000Plus Bondtester
5 Pages
-
4000 Optima Bondtester
5 Pages
-
Micro Materials Testing
5 Pages
-
Paragon Bondtesting Software
5 Pages
-
PCI™ Controller
2 Pages
-
Process Sentry™
2 Pages
-
Rhino® VE Bulk Unloaders
2 Pages
-
Trilogy™ AAA-LT Manual
2 Pages
-
Nordson Diaphragm Pumps
4 Pages
-
Power Catalog
447 Pages
-
Controlled Pressure (CP) Gun
2 Pages
-
AccuDrop™ Gun
2 Pages
-
Auto-Flo™ Dispensing Valves
2 Pages
-
CE20 Valve
2 Pages
-
2151-482 Series Valves
2 Pages
-
2600-093 Series Valves
1 Pages
-
CoolWave® 2
2 Pages
-
CoolWave®
2 Pages
-
Anti-Static Powder Tubing
1 Pages
-
1209-530 Series
2 Pages
-
Servo-Flo® 704
2 Pages
-
Model EP II Pumping System
2 Pages
-
Flow Coat Primer System
2 Pages
-
Liquid Coating Systems Catalogue
16 Pages
-
VersaPail Bulk Melters
2 Pages
-
DuraDrum® Bulk Melters
2 Pages
-
Airless Nozzle Catalog
202 Pages
-
Model 25B Pump
2 Pages
-
RA-20 Rotary Atomiser Cups
2 Pages
-
Nordson Oscillator
2 Pages
-
Gun Mover
4 Pages
-
MicroMax Booth
4 Pages
-
Cartridge Booths
2 Pages
-
StediTherm Fluid Heaters
2 Pages
-
OptiMix IV
2 Pages
-
Optimix III
2 Pages
-
OptiMix II
2 Pages
-
OptiMix I
2 Pages
-
Trilogy AAA Dolly Systems
2 Pages
-
Trilogy AAA-LT
2 Pages
-
Trilogy AC Manual
2 Pages
-
Trilogy GP Manual
2 Pages
-
Trilogy AAA Automatic
2 Pages
-
Trilogy AS and LVLP Manual
2 Pages
-
Trilogy AAA Manual
2 Pages
-
High Pressure Fluid Filters
2 Pages
-
Automotive Assembly Systems
8 Pages
-
PermaFlo® Series Pumps
4 Pages
-
64B Pumps
2 Pages
-
A7A Colour Change Valves
2 Pages
-
NH-4 Heater
2 Pages
-
Temperature Control Unit
2 Pages
-
ISC2 Pre-Cure Oven
2 Pages
-
EcoDry® Compound Dryer
4 Pages
-
Can End Sterilizers
2 Pages
-
EcoLiner Compound Gun
2 Pages
-
A20A Electric Spray Gun
2 Pages
-
MEG® Inside Stripe
2 Pages
-
MEG® II Compact Spray Gun
2 Pages
-
Rhino® Bulk Unloader
2 Pages