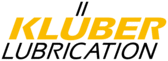
Group: Freudenberg

Catalog excerpts
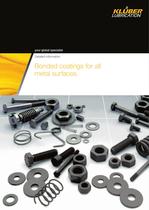
your global specialist Detailed information Bonded coatings for all metal surfaces.
Open the catalog to page 1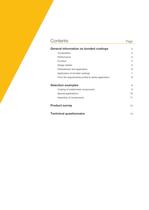
General information on bonded coatings 3 Application of bonded coatings 7 From the requirements profile to series application 8 Coating of metal/metal components 9
Open the catalog to page 2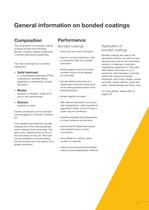
General information on bonded coatings Composition Performance The composition of a bonded coating is similar to that of an ndustrial i lacquer, however instead of pigments it contains lubricating substances. Bonded coatings The main constituents of a bonded coating are: – olid lubricant S e. g. polytetrafluoroethylene (PTFE), molybdenum disulfide (MoS2), g raphite or a combination of solid lubricants – inder B (organic or inorganic, made up of one or two components) – olvent S (organic or water) Further constituents are for example coloring agents or corrosion inhibitors etc. Once...
Open the catalog to page 3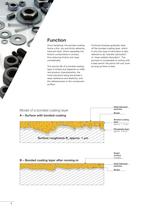
Once hardened, the bonded coating forms a thin, dry and firmly adhering lubricant layer, which separates the friction components in contact, thus reducing friction and wear The service life of a bonded coating layer is limited and depends on diffe- rent product characteristics, the most important being the binder's wear resistance and elasticity, and Frictional stresses gradually wear off the bonded coating layer, which is why this type of lubrication is also referred to as "transfer lubrication" process is comparable to writing with a lead pencil: the pencil will only work as long as there...
Open the catalog to page 4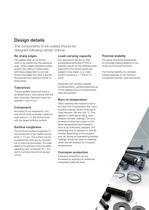
Design details The components to be coated should be designed following certain criteria: No sharp edges Load-carrying capacity Thermal stability This applies both to the friction body to be coated and the opposing body. Sharp-edged opposing bodies scratch the coating. Coated parts with sharp edges tend to corrode around the edges and have a shorter life because the coating is thinner in these areas. Our experience has shown that p olytetrafluoroethylene (PTFE) or graphite should be the preferred solid lubricants if the friction points are s ubject to low loads, e. g. mean surface...
Open the catalog to page 5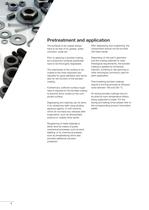
Pretreatment and application The surfaces to be coated always have to be free of oil, grease, water, corrosion, scale etc. After degreasing and roughening, the components should not be touched with bare hands. Prior to applying a bonded coating, the component surfaces (substrate) have to be thoroughly degreased. Depending on the part’s geometry and the coating selected to meet t ribological requirements, the bonded coating is applied by immersion, i njection, tumbling or dip-spinning or other techniques commonly used for paint application. The cleanliness of the surface to be coated is...
Open the catalog to page 6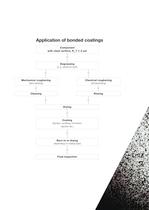
Application of bonded coatings with clean surface, R = 1-2 um Mechanical roughening (sand blasting) Chemical roughening (dip/spin, tumbling, immersion, (depending on coating type) Final inspection
Open the catalog to page 7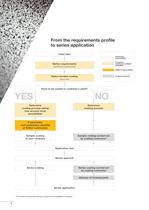
From the requirements profile Initial idea Define requirements (technical questionnaire) Select bonded coating Kluber's responsibility Coating contractor coating process taking into account local coating process coat preliminary samples Sample coating Sample coating carried out Application test Series approval Series coating Series coating carried out Delivery of finished part Series application The names of potential coating contractors are available on request.
Open the catalog to page 8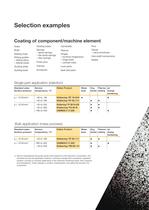
Selection examples Coating of component/machine element Sealing rings Sliding guides - sliding discs - sliding tubes Guiding axles Guiding bolts Guiding tubes - spiral springs - flat spiral springs - disc springs Chain pins - furniture hinges/pins - hinge bolts - cylinder bolts Lock parts Seat belt parts - valve armatures Hub-shaft connections Single-part application (injection) Bulk application (mass process) 1) Service temperatures are guide values which depend on the lubricant's composition, the intended use and the application method. Lubricants change their consistency, apparent...
Open the catalog to page 9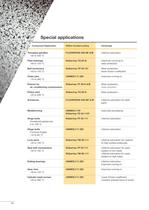
Kliiber bonded coating Lifetime lubrication for steel Metalforming UNIMOLY CP Improved processing Seat belt mechanisms Klubertop TP 03-111 Lifetime lubrication for parts Klubertop TM 06-111 Lifetime lubrication for parts subject to high loads Cylinder head screws UNIMOLY C 220 Lower friction coefficient, -40 to 260 °C constant preload force of screw
Open the catalog to page 10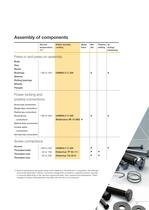
Assembly of components Service Klüber bonded Water Bin- Thermo- air temperature, coating base der setting drying/ °C1) hardening Press-in and press-on assembly Bolts Pins Rivets Bushings –180 to 450 UNIMOLY C 220 • • UNIMOLY C 220 • • • • • • • • Sleeves Rolling bearings Wheels Flanges Power-locking and positive connections Screw-bolt connections Wedge-type connections Feather key connections Woodruff key –180 to 450 connections (Klüberplus SK 12-205) • Splined shaft connections Involute spline connections Serrated hub connections Screw connections Screws –180 to 450 Threaded bolts –40 to...
Open the catalog to page 11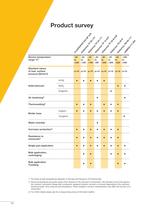
Product survey Bulk application *) The stress at high temperatures depends on the type and frequency of fhctional load. 1) Service temperatures are guide values which depend on the lubricant's composition, the intended use and the applica- tion method. Lubricants change their consistency, apparent dynamic viscosity or viscosity depending on the mechano- dynamical loads, time, pressure and temperature. These changes in product characteristics may affect the function of a 2) For further details please see the corresponding product information leaflets.
Open the catalog to page 12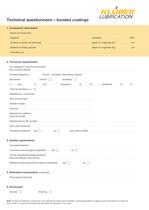
Technical questionnaire - bonded coatings Surface condition as delivered Is it possible to coat the entire part? Surface pressure p= N/mm2 (constant, alternating, impact) Movement uniform Q oscillating O Corrosion around edges acceptable: yes Q no Q Further requirements/specifications/ Reference data required for subject component: yes Q no O Note: At least one reference sample has to be retained for internal documentation. Series application is subject to prior manufacture of a pilot lot (the number of components depends on the respective geometry of the part).
Open the catalog to page 14All Klüber Lubrication catalogs and technical brochures
-
KlueberEfficiencySupport
7 Pages
-
Klübermatic lubricant dispensers
13 Pages
-
Driving with Klüber Lubrication.
15 Pages
-
Geared up for success.
32 Pages
-
All sprays at a glance
2 Pages
-
Automotive industry
16 Pages
-
Cement industry
2 Pages
-
Tribojournal edition 1 - 2011
32 Pages
-
Seaworthy
24 Pages
-
Pneumatics
24 Pages