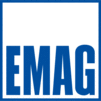

Catalog excerpts
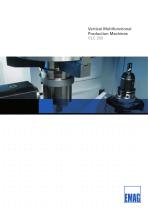
Vertical Multifunctional Production Machines VLC 250
Open the catalog to page 1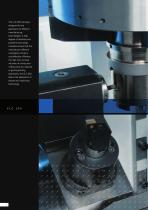
The VLC 250 has been designed for the application of different manufacturing technologies. A high degree of flexibility and powerful technology modules ensure that the manufacture different workpieces remains cost effective. Whether the high chip removal volumes of turning and milling work are required or gentle grinding operations, the VLC 250 allows the application of almost any machining technology.
Open the catalog to page 2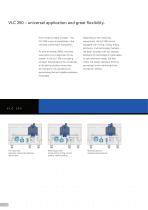
VLC 250 – universal application and great flexibility. From simple to highly complex – the universal machining of workpieces. equipped with turning, milling, drilling, grinding or multi-technology modules – As with all vertical EMAG machines, the latter complete with tool changer. automation is an integral part of the Decisions for technology is made based on the customers needs. The final conveyor belt transports the workpieces choice will always represent the best to the pick-up position where they are clamped in the spindle chuck, workpiece involved. guaranteeing fast and reliable...
Open the catalog to page 4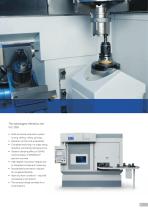
The advantages offered by the VLC 250 • Multi-functional production system: turning, drilling, milling, grinding, … • Operator comfort and accessibility • Complete-machining in a single setup, therefore, eliminating clamping errors • Vibration damping effect on EMAG machine bases in MINERALIT® polymer concrete • High degree of process integrity due to integrated component measuring • Standardized automation modules for increased flexibility • Ideal chip flow conditions – chips fall unhindered to the bottom • The compact design provides fo
Open the catalog to page 5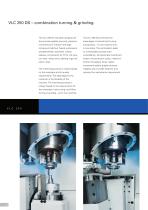
The VLC 250 DS has been designed for the process-capable, low-cost, precision manufacture of medium and large component batches. Typical workpieces are gearwheels, sprockets, sliding sleeves, components for CVTs, link pins, con-rods, rocker arms, bearing rings and piston rings. The machining process is chosen based on the workpiece and its quality requirements. The advantage for the customer is the flexibility of the machine. The machining process is chosen based on the requirements for the workpiece: hard turning, scroll-free turning or grinding - all on one machine. The VLC 250 DS...
Open the catalog to page 6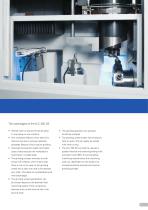
The advantages of the VLC 250 DS • Vertical hard turning and finish-grinding in one setup on one machine • Any workpiece feature which allows for hard turning due to process reliability precedes features which require grinding • Improved component quality and higher output rates because the workpiece is machined in a single setup • The grinding process removes a small amount of material, which means that there is not much wear to the grinding wheel and it does not have to be dressed very often. This leads to considerable cycle time advantages • The grinding wheel specification can be chosen...
Open the catalog to page 7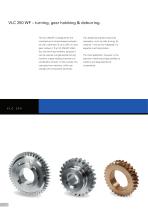
VLC 250 WF – turning, gear hobbing & deburring. If an additional operation becomes manufacture of wheel-shaped workpiec- necessary– such as roller burring, for instance – this can be integrated in a gear module 4. The VLC 250 WF offers separate machining station. the user the most flexibility, because it can be used as a single-spindle turning The main application, however, is the machine, a gear hobbing machine or a precision machining of gear profiles on combination of both. In other words, the medium and large batches of user gets two machines, which can change with component demands.
Open the catalog to page 8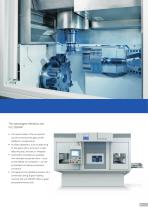
The advantages offered by the VLC 250 WF • The second side of the component can be turned and the gear profile hobbed in a single setup • Auxiliary operations, such as deburring of the gears with a turning or a roller deburring tool, are easy to integrate • Automation concepts are available with directed component flow – such as the EMAG InLine System – as well as standard circulating component conveyors • Compared to the traditional solution of a combined turning & gear hobbing machine the VLC 250 WF offers a great price-perform
Open the catalog to page 9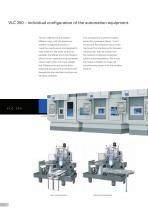
VLC 250 – individual configuration of the automation equipment. This arrangement is great for a batch different ways, with the equipment production, because it allows “in-line” content configured according to component flow between two or three customer requirements and designed to machines. The interface points between keep travel and idle times as short as machines can then be utilized with possible. The EMAG ILS (InLine System) the insertion of optional component allows for the machines to be positioned buffers or docking stations. This is how close to each other, forming a straight ILS...
Open the catalog to page 10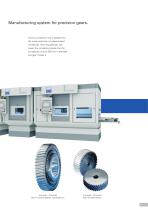
Manufacturing system for precision gears. The VLC production line is designed for the mass production of wheel-shaped workpieces, featuring gearings, and covers the complete process chain for workpieces of up to 200 mm in diameter and gear module 4. Line speed – 42 seconds Gear for a manual gearbox in passenger cars Line speed – 24 seconds Gears for speed reducers
Open the catalog to page 11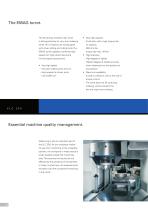
The fast acting 12-station disc turret is distinguished by its very short indexing times. All 12 stations can be equipped with driven drilling and milling tools. The EMAG turret's gearbox combines high speed with high performance and minimal space requirement. • Very high speed ■ Very fast indexing time of 0.3 s ■ High speeds for driven tools: max 6,000 rpm • Very high capacity ■ Small size, with a high torque rate: 12 stations, 360 mm dia., torque rate max. 40 Nm • High precision ■ High degree of rigidity ■ Highest degree of repeat accuracy when indexing from tool position to tool...
Open the catalog to page 12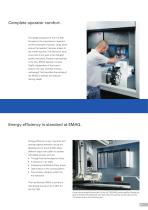
The design engineers of the VLC 250 focused on the importance of operator comfort and ease of access. Large doors ensure the operator has easy access to the machining area. This allows for tools, chuck and chuck jaws to be changed quickly and easily. Another improvement is the new EMAG operator console. Totally independent of the control system, the user interface remains unchanged. This simplifies the setting of the EMAG machines and reduces training needs. Energy efficiency is very important and received special attention during the development of the VLC 250. Many different steps were...
Open the catalog to page 13All EMAG GmbH & Co. KG catalogs and technical brochures
-
VL-SERIES
16 Pages
-
Hardening Systems
12 Pages
-
Joining Machines
12 Pages
-
ECM-/PECM-Machines
16 Pages
-
Laser-Welding Machine - ELC 160
20 Pages
-
Gear Hobbing Machine - VLC 200 H
12 Pages
-
Gear Hobbing Machine - K 300
12 Pages
-
Gear Hobbing Machine - K 200
12 Pages
-
Gear Hobbing Machines - K 160
12 Pages
-
Machining Centers - VLC
20 Pages
-
Machining Centers - VM series
16 Pages
-
Grinding Machine - HG 2
8 Pages
-
Grinding Machine - SN 204-208
12 Pages
-
Grinding Machine - VG 110
16 Pages
-
Grinding Machine - SK 204
8 Pages
-
Grinding Machine - PM 310-320
12 Pages
-
Grinding Machine - PM 2
8 Pages
-
Turning Machine - VTC 315 DS
12 Pages
-
Turning Machine - VTC
16 Pages
-
Turning Machine - VTC 100 GT
4 Pages
-
Turning Machine - VT
8 Pages
-
Turning Machine - VSC DUO twin
24 Pages
-
Turning Machines - VSC
20 Pages
-
Turning Machine - VMC
12 Pages
-
Turning Machine - VM
4 Pages
-
Turning Machines - VL
16 Pages
-
Vertical grinding machine VG 110
16 Pages
-
VERTICAL TURNING MACHINES
20 Pages
-
ELC Laser Welding Systems
20 Pages
-
ECM / PECM Technology
20 Pages
-
Product Summary EMAG Group
36 Pages
-
Crankshaft grinder PM2
8 Pages
-
Crankshaft grinder PM310/320
12 Pages