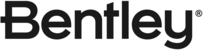

SACS Enables L&T-Valdel to Deliver Optimized FPSO Design and Meet Accelerated Project Schedule
2Pages
Catalog excerpts
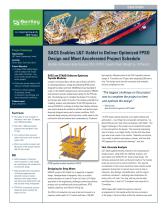
CASE STUDY Project Summary Organization: L&T-Valdel Engineering Limited Location: Santos Basin, Sao Paulo, Brazil Project Objective: • Complete FPSO topside design with 15 modules and 10 pipe racks within 10 months – two to four months quicker than for similar projects. • Perform pre-service analysis of lift, load-out, and barge transportation. • Perform in-service analysis of operating, survival, no-shutdown, ship damage, and ship transportation conditions. Products used: SACS, STAAD.Pro Fast Facts • The scope of work involved six disciplines, more than 120 people, and 2,000 deliverables. SACS Enables L&T-Valdel to Deliver Optimized FPSO Bentley InRoads Design and Meet Accelerated Project Schedule ® Powerful tools for the design of civil infrastructure Bentley Software Helps Reduce OSX-3 FPSO Topside Steel Weight by 10 Percent SACS and STAAD Software Optimizes Topside Modules Located in the Santos Basin off the coast of Brazil, the OSX-3 is a floating production, storage and offloading (FPSO) vessel designed to produce and treat 100,000 barrels per day (bpd) of crude oil. L&T-Valdel Engineering was commissioned by MODEC International to provide modularization design for the FPSO topside. The challenge was to complete the design of 15 modules and 10 pipe racks within 10 months. The company used SACS for modeling, analysis, and optimization of the FPSO topside structure and STAAD.Pro to design its tertiary steel. Bentley software was used to analyze the module for all static and dynamic loads observed during pre-service and in-service conditions. SACS improved design accuracy and visual clarity, which saved on-site construction time and reduced steel consumption by 10 percent. • More than 1,000 special pipe supports were designed in just 15 days. • First cutting of steel occurred within three-and-a-half months of project start. • Within six months of project start, 80 percent of the overall material take off was issued. • SACS provided clear visualization of lifting arrangements and detected structural clashes, helping to avoid major rework and saving time finalizing the safe and practical lifting arrangement. • STAAD.Pro’s speed and accuracy helped the team complete the project on time. “The biggest challenge on this project was to complete the project on time and optimize the design.” — Sharad Jain, lead structural engineer, L&T-Valdel “An EPC project always demands a very tight schedule and optimization – two things that are basically contradictory,” explained Sharad Jain, lead structural engineer, L&T-Valdel. “The biggest challenge on this project was to complete the project on time and optimize the design.” The structural engineering was to be done in just eight months, and the first steel drawings were to be issued in four months. “Basically we had only four months to perform optimization, analysis, and have final AFC (approved for construction) drawings,” said Jain. Fast, Accurate Analysis ROI • SACS achieved a 10 percent overall reduction in steel weight per module/pipe rack compared to conventional design. bpd capacity. Modularization of the OSX-3 topsides involved design of 15 modules and 10 pipe racks weighing 6,000 metric tons. The design had to be both economical and workable, and also completed on time. FPSO topsides module modeled in SACS Designing for Deep Water MODEC turned to L&T-Valdel for its expertise in topsides design. Headquartered in Bangalore, India, as a wholly owned subsidiary of Larsen & Toubro Ltd, India, L&T-Valdel specializes in the engineering challenges confronting offshore projects such as wellhead and process platforms, FPSO topsides, pipelines, and offshore drilling rigs. The OSX-3 oil production ship was to be turret-moored in a maximum water depth of 110 meters and have a 100,000 L&T-Valdel applied Bentley software to the modularization design process, using SACS for modeling, analysis, and optimization and STAAD.Pro for tertiary steel design. The software analyzed all static and dynamic loads on the module under pre-service and in-service conditions. This required consideration of the various conditions these modules would experience during their in-service tenure such as ship acceleration, ship damage, ship deflections, and the support conditions considered – analyzing load combinations for heave, pitch, roll, heel, trim, hog, and sag, plus all eight wind directions. A total of 175 analyses were required for 25 modules. SACS helped L&T-Valdel find optimum structural arrangements for the topside within the time constraints of the project. Various utilities within the software were used
Open the catalog to page 1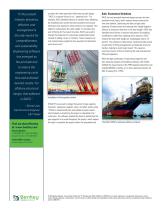
“In the present industry dynamics, effective cost management is the only mantra for competitiveness and sustainability. to reduce the steel quantities while ensuring safe design. “SACS is a natural choice for us,” explained Jain. “For example, SACS identified failures at member ends. Modeling the modified joints solved the failure problems that would otherwise have required a whole section to be replaced. This helped in cutting down the steel weight. To provide minor axis stiffening for the overall structure, SACS was used to change the properties of a previously modeled deck plate instead...
Open the catalog to page 2All Bentley Systems Europe B.V. catalogs and technical brochures
-
Digital Airport Project Showcase
18 Pages
-
Water_Hazelwood_Coal_Mine
2 Pages
-
Water_Simtejo_case_study
2 Pages
-
Wimbledon Stadium_Case Study
2 Pages
-
WSP-Shard_Case_Study
3 Pages
-
Bentley’s Water Project Showcase
92 Pages
-
Mine Water Software Solution
4 Pages
-
AutoPLANT Equipment V8i
2 Pages
-
AutoPLANT Piping V8i
2 Pages
-
ConstructSim
2 Pages
-
promis•e
2 Pages
-
Bentley Datasheets
2 Pages
-
Making PDS Interoperable
17 Pages
-
Bentley OpenPlant PowerPID
2 Pages
-
STAAD.Pro
2 Pages
Archived catalogs
-
Water modelling
24 Pages
-
Bentley Water V8 XM
2 Pages
-
Bentley Cadastre Specsheet
2 Pages
-
STAAD Foundation
2 Pages
-
RAM CADStudio
2 Pages
-
Bentley MAP
2 Pages
-
Bentley Structural Brochure
2 Pages
-
Bentley Project Yearbook 2006
82 Pages
-
Bentley SewerCAD
2 Pages
-
Bentley WaterCAD
2 Pages
-
Bentley WaterGEMS
2 Pages
-
Bentley HAMMER
2 Pages
-
Bentley StormCAD
2 Pages
-
Bentley SewerGEMS
2 Pages
-
Bentley AutoPlant P&ID
2 Pages
-
Bentley Microstation
2 Pages
-
Bentley Architecture
2 Pages
-
Bentley ProjectWise brochure
2 Pages
-
Bentley CivilStorm
2 Pages
-
Bentley ProjectWise
4 Pages
-
Bentley PowerDraft
2 Pages
-
Bentley AutoPipe Specsheet
2 Pages